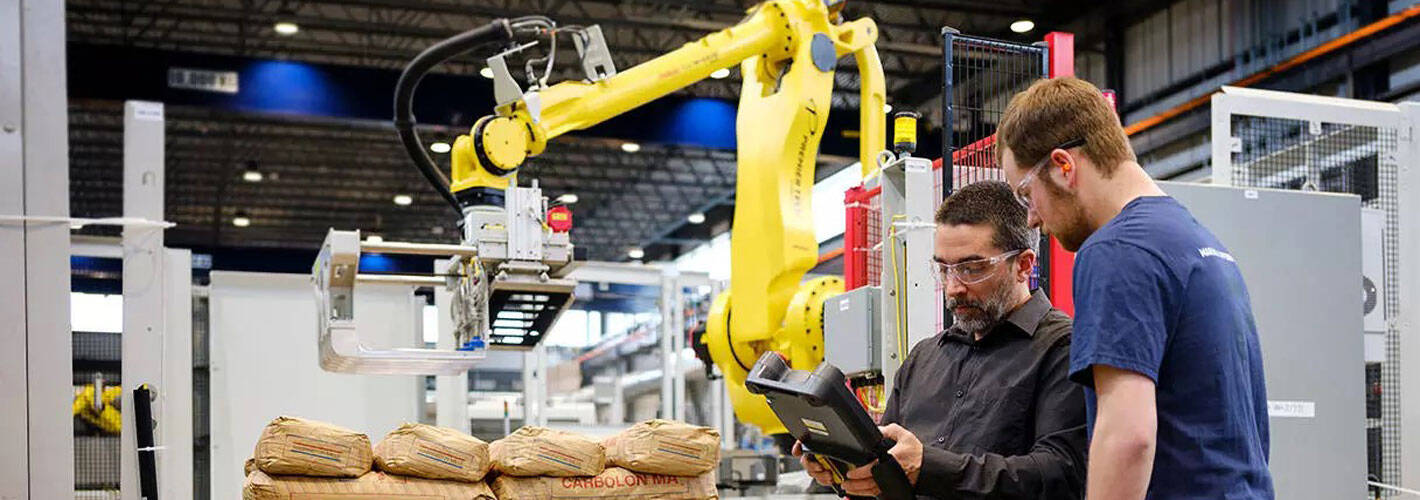
Avant d’investir dans un palettiseur robotisé, lisez d’abord ce guide
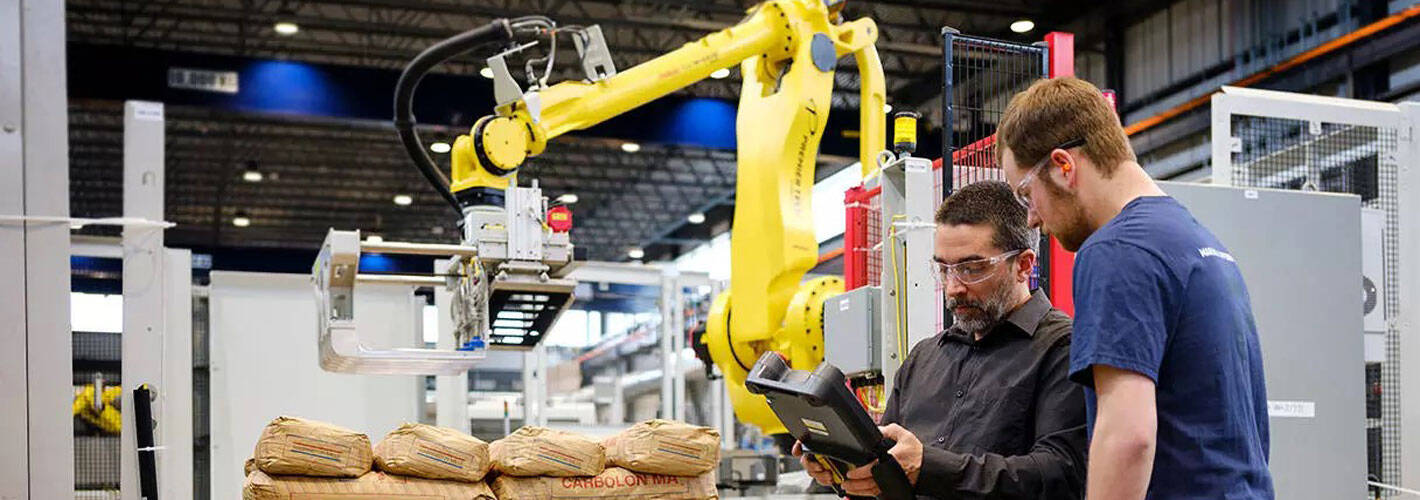
Tous les palettiseurs robotisés ne sont pas construits de la même manière, et le choix du robot approprié ne se limite pas à une comparaison des caractéristiques de la charge utile ou des étiquettes de prix.
Certains systèmes sont prêts à l’emploi. D’autres nécessitent une ingénierie complexe. Certains s’intègrent dans des espaces plus restreints, tandis que d’autres occupent la moitié de votre superficie de plancher.
Ce guide présente tout ce qu’il faut savoir sur la question, depuis les types de systèmes proposés et les scénarios d’utilisation en conditions réelles jusqu’à l’intégration, la sécurité et les coûts. Que vous automatisiez pour la première fois ou que vous développiez les produits déjà en place, ce guide vous aidera à déterminer le système qui convient, celui qui ne convient pas et les raisons connexes.
Veillez à poser les bonnes questions avant d’investir dans un palettiseur robotisé.
Qu’est-ce qu’un palettiseur robotisé ?
Un palettiseur robotisé met en œuvre un bras robotisé pour empiler des produits sur une palette. Le robot peut ramasser des articles un par un, en rangées ou par couches entières, en fonction de l’outil fixé sur le bras. Certains systèmes intègrent également une technologie de vision, qui aide le robot à placer les articles avec plus de précision, voire à faire se chevaucher des sacs, si nécessaire.
Avez-vous besoin d’un palettiseur robotisé ? (dans quel cas n’en avez-vous pas besoin)
Investir dans la palettisation robotisée peut offrir de grands résultats. Mais elle ne constitue pas toujours la bonne solution pour tous les établissements. Certaines opérations ne se prêtent tout simplement pas encore à l’automatisation, et mettre en œuvre cette dernière trop tôt peut créer plus de problèmes qu’elle n’en résout.
Moyen de vérifier rapidement la pertinence de l’automatisation
Posez-vous les questions suivantes pour déterminer si la palettisation robotisée est adaptée à votre activité :
- Sommes-nous constamment en retard en ce qui a trait à la palettisation ?
- Avons-nous du mal à pourvoir les postes de palettiseurs, en particulier pour les équipes du soir ou de la fin de semaine ?
- Avons-nous consigné des blessures ou des plaintes liées à des tâches répétitives de levage ou d’empilage ?
- Faut-il augmenter le débit sans augmenter les effectifs ?
- Des palettes incompatibles ou un mauvais empilage entraînent-ils des refus de chargement ou des problèmes d’expédition ?
- Le fait de retirer des employés des tâches de palettisation répétitive les libérerait-il pour des fonctions plus qualifiées ou plus flexibles ?
Si vous avez répondu « oui » à la plupart de ces questions, votre entreprise se prête vraisemblablement bien à la palettisation robotisée.
Avantages et inconvénients
Comme tous les outils, les palettiseurs robotisés ont des avantages et des inconvénients. Voici une analyse sommaire qui vous aidera à prendre votre décision.
Avantages des palettiseurs robotisés
- Qualité constante des chargements et précision de l’empilage pour toutes les équipes et tous les numéros d’article
- Réduction des risques ergonomiques liés au levage répétitif et à la manutention de charges lourdes
- Libération de la main-d’œuvre qualifiée pour des tâches à plus forte valeur ajoutée comme l’installation des équipements ou l’assurance qualité
- Évolution du débit en fonction de la croissance saisonnière ou à long terme de la production
- Capacité à travailler dans des quarts entièrement automatisés ou pendant des déficits de main-d’œuvre sans supervision
- Possibilité de bénéficier de subventions gouvernementales ou industrielles liées à des gains en matière de sécurité ou de productivité
Aspects à prendre en compte et limites concernant les palettiseurs robotisés
- Coût d’investissement initial et délai d’approvisionnement et d’installation
- Nécessité éventuelle de redéfinir l’agencement pour tenir compte de la portée, des besoins en protection ou du rendement des robots
- Formation requise pour les opérateurs et le personnel d’entretien concernant la gestion du système
- Moins adaptés aux UGS à faible volume ou aux configurations de charge particulièrement variables/imprévisibles
Le type de système de palettisation que vous choisissez peut avoir des répercussions importantes sur la complexité ou la durée de votre projet. Il est utile de bien cerner les différents types de systèmes afin de choisir celui qui correspond à votre calendrier, à vos ressources et à vos objectifs.
Types de palettiseurs robotisés
Les palettiseurs robots sont proposés dans toute une série de configurations, depuis les systèmes de base jusqu’aux systèmes entièrement automatiques conçus pour une production ininterrompue. Le bon choix dépend de votre volume à traiter, de votre encombrement et de la quantité de manipulations manuelles que vous souhaitez éliminer.
Systèmes robotisés de base
Il s’agit des formes les plus simples de palettiseurs robots. Ces palettiseurs vous offrent les avantages de l’automatisation sans la complexité ni le coût d’un système entièrement intégré.
Un système de base comprend généralement :
- Un bras robotisé
- Un outil en bout de bras
- Un transporteur d’entrée
- Une clôture de sécurité ou des numériseurs de zone
Ce qui manque, c’est l’automatisation au-delà du processus d’empilage. Il n’y a pas de distributeur de palettes ni de distributeur de feuilles de palettisation.
La palette est généralement posée sur le sol et doit être enlevée à l’aide d’un chariot élévateur à fourche ou d’un chariot à main. Chaque fois qu’une palette est pleine, le système se met en pause jusqu’à ce qu’un technicien place une palette vide.
Les systèmes de base peuvent réduire les opérations manuelles de levage et améliorer l’homogénéité des piles, mais ils nécessitent toujours des interventions périodiques de la part des opérateurs.
Systèmes robotisés entièrement automatiques
Ces systèmes sont conçus pour fonctionner en continu avec peu voire aucune intervention manuelle. Ils peuvent palettiser à grande vitesse, manipuler différents types de produits et effectuer des changements d’équipe sans interruption.
Un système entièrement automatique comprend :
- Un bras robotisé
- Un outil en bout de bras
- Un transporteur d’entrée
- Un distributeur de palettes
- Un distributeur de feuilles de palettisation
- Une clôture de sécurité ou des numériseurs de zone
- Un convoyeur de sortie qui déplace les palettes pleines vers une station d’emballage ou une zone de transfert
Voici comment cela fonctionne :
Les produits sont acheminés sur le convoyeur d’entrée. Le distributeur de palettes charge une palette vide en position. Une feuille de palettisation peut être placée en premier. Le robot commence ensuite à empiler les articles, rangée par rangée ou couche par couche. Une fois le processus terminé, la palette pleine est transférée vers la sortie, et le processus se répète automatiquement.
L’un des principaux avantages de ces systèmes est qu’il est possible de recharger le magasin de palettes sans arrêter le système. Cette seule tâche permet d’économiser des heures d’immobilisation au cours d’une semaine.
Technologies des palettiseurs robots
Tous les palettiseurs robots n’utilisent pas le même type de bras robotisé. Les deux principales options sont les robots industriels traditionnels et les robots de collaboration (cobots). Chacun d’entre eux présente ses propres avantages et est adapté à des environnements différents.
Les bras robotisés traditionnels sont plus rapides, supportent des charges utiles plus lourdes et sont généralement utilisés dans des systèmes entièrement automatiques à rendement élevé. Ils nécessitent des clôtures de sécurité ou des barrières immatérielles et davantage d’espace physique.
Les cobots sont conçus pour travailler en toute sécurité aux côtés des employés et disposent de fonctions de sécurité intégrées comme la limitation de la force et de la vitesse. Ils ne nécessitent pas une protection complète, ce qui les rend particulièrement adaptés aux zones de travail réduites ou aux opérations où l’homme doit interagir étroitement avec la cellule.
La technologie collaborative s’avère très utile dans les usines dont l’espace au plancher est limité ou dont les besoins de production évoluent.
Ce que l’on recherche dans un palettiseur robotisé
La qualité d’un palettiseur robot dépend de celle de ses différents composants. Pour choisir le bon logiciel, il faut savoir à quoi prêter attention; il faut d’abord se pencher sur le bras et vérifier la façon dont votre équipe interagit avec le logiciel.
Le bras : charge utile, portée et commande
Chaque palettiseur robotisé comporte un bras. Les deux types de robots les plus courants sont les robots industriels traditionnels et les robots de collaboration, encore appelés « cobots ».
Les bras robotisés industriels peuvent soulever des charges utiles plus lourdes et se déplacer plus rapidement. Ils sont le robot idéal pour les environnements à débit élevé, mais nécessitent généralement plus d’espace et de dispositifs de sécurité.
Les cobots sont conçus pour travailler en toute sécurité à proximité des personnes. Leur capacité de charge est plus faible et leur vitesse plus lente, mais ils sont moins encombrants et peuvent souvent fonctionner sans clôture.
Au moment de comparer les bras, il est important de tenir compte des caractéristiques suivantes :
- Capacité de charge : Poids que le bras peut soulever par prise
- Portée : Distance à laquelle le bras peut s’étendre depuis sa base
- Commande des axes : Nombre d’articulations et manière dont elles permettent de positionner ou de faire pivoter la charge
Ces caractéristiques déterminent les types de produits que vous pouvez manipuler, la vitesse à laquelle vous pouvez les déplacer et si le robot peut atteindre un ou plusieurs emplacements de palettes.
Outil de bout de bras (EOAT)
Il s’agit du préhenseur qui exécute le travail. Autrement dit, c’est l’outil terminal qui détermine ce que le robot peut soulever, la fiabilité avec laquelle il place les objets et s’il peut s’adapter à différentes formes de produits ou de matériaux.
Voici les types de préhenseurs les plus courants et ce à quoi ils servent :
- Préhenseur à serrage : Consiste en des plaques métalliques conçues pour serrer les deux côtés d’un sac ou d’une boîte avant de les soulever. Accessoire idéal pour les produits rigides ou emballés.
- Préhenseur à doigts : Glisse les dents sous les côtés d’un produit. Souvent utilisé pour des sacs de différentes tailles et des matériaux différents.
- Préhenseur à fourche : Permet de soulever les boîtes à dessus ouvert ou les grands sacs par le bas. Idéal pour les objets surdimensionnés ou non stables.
- Préhenseur magnétique : Permet de ramasser les pièces métalliques telles que les boîtes de conserve ou les matériaux de construction sans les endommager.
- Préhenseur à seau : Spécialement conçu pour soulever des seaux en plastique ou en métal en les saisissant juste en dessous du couvercle.
- Préhenseur à anneau : Permet de soulever des fûts ou de grands conteneurs ronds par le haut au moyen d’un accessoire circulaire.
- Préhenseur pour feuilles de palettisation : Accessoire pratique permettant au robot de positionner des feuilles de palettisation ou des palettes en plus des produits.
- Préhenseur à ventouse : Utilise le vide pour soulever délicatement les objets par le haut. Utile pour les produits fragiles ou légers.
Le choix du bon préhenseur dépend de ce que vous palettisez, de sa fragilité et de la diversité de votre catalogue de produits.
Logiciel de palettiseur robotisé
Le robot est le muscle. Le logiciel est le cerveau.
Il est important de rechercher un logiciel de palettisation qui simplifie la création de modèles, et non un logiciel qui ajoute de la complexité. Les interfaces « glisser-déposer », les éditeurs visuels et les ajustements basés sur l’IA peuvent aider votre équipe à mettre en place et à actualiser les programmes sans avoir besoin de coder.
Si vous gérez plusieurs UGS ou si vous devez changer souvent de modèle de palette, assurez-vous que le logiciel vous facilite également la tâche.
Systèmes de vision pour palettiseurs robotisés
Dans les applications de palettisation, les systèmes de vision garantissent la précision, la souplesse et un temps de fonctionnement constant, en particulier dans les environnements de production dynamiques.
La vision intégrée permet au robot de localiser, d’identifier et d’orienter les produits en temps réel. Cette fonctionnalité est précieuse lorsque l’on doit gérer :
- une caractéristique de présentation non conforme du produit à l’entrée, comme un espacement ou une orientation variable;
- des emballages souples ou déformables, y compris les sacs de polyéthylène ou les plateaux emballés sous film rétractable;
- des palettes UGS mixtes, où le robot doit différencier et placer avec précision plusieurs types de caisses.
La vision permet au système de s’adapter dynamiquement aux variations liées au produit, ce qui réduit le besoin de retouches physiques ou d’arrêts de ligne. Elle permet d’assurer ce qui suit :
- l’alignement correctif en temps réel;
- un temps de cycle plus rapide en éliminant les retards dus aux erreurs d’alimentation;
- une réduction des interventions de l’opérateur, en particulier lorsque les articles changent fréquemment.
Vision-equipped palletizers maintain performance even with variability on the line, helping operations stay efficient without over-engineering mechanical controls.
Sécurité : Clôtures, numériseurs et aspects liés à l’aménagement
La sécurité ne se limite pas au respect de la réglementation. Elle concerne également l’espace au sol et la conception du système.
Les robots traditionnels doivent généralement être entièrement protégés par des clôtures et des dispositifs de verrouillage.
Les cobots utilisent des dispositifs de sécurité intégrés variés, comme des dispositifs de limitation de force et de vitesse, pour fonctionner dans des espaces partagés.
Des barrières immatérielles et des numériseurs de zone sont souvent utilisés avec les robots et les cobots pour mieux protéger les personnes se trouvant à proximité, sans pour autant isoler la cellule.
Plus votre système est sûr du fait de sa conception, moins il perturbe votre sol. Si vous travaillez dans un endroit étroit ou très fréquenté, cela fait une grande différence.
Sécurité : Conception de la cellule, évaluation des risques et zonage fonctionnel
L’automatisation de la palettisation nécessite une conception réfléchie de la sécurité qui concilie la protection de l’opérateur, l’efficacité du flux de travail et l’optimisation de l’espace.
Les robots industriels traditionnels fonctionnent généralement dans des cellules de sécurité entièrement fermées, équipées de clôtures verrouillées, de portes de sécurité et de dispositifs d’arrêt d’urgence pour répondre aux exigences de niveau de rendement (NR).
Les palettiseurs collaboratifs intègrent des fonctions de limitation de puissance et de force (LPF), ce qui permet aux palettiseurs de travailler à proximité du personnel. Cela dit, une évaluation des risques propres à la tâche est toujours nécessaire pour déterminer le niveau de protection approprié pour l’ensemble de l’application, et pas seulement pour le bras du robot.
Les systèmes modernes comprennent souvent des numériseurs de zone, des barrières ou des tapis de sécurité pour définir des zones de sécurité fonctionnelles qui limitent l’accès en cas de mouvement tout en maintenant la visibilité directe et en réduisant au minimum l’utilisation de l’espace. Ceci est particulièrement utile dans les environnements de fin de ligne où l’espace au sol est limité et où le flux de circulation est élevé.
Une architecture de sécurité bien conçue garantit la conformité aux normes ISO 10218 et TS 15066 tout en permettant une mise en service rapide, une conception d’agencement efficace et une convivialité à long terme dans l’atelier de production.
Scénarios d’utilisation des palettiseurs robotisés
Les palettiseurs robotisés (ou palettiseurs robots) peuvent exécuter un large éventail de tâches, mais les meilleurs systèmes sont construits en ayant à l’esprit des objectifs très précis. Qu’il s’agisse de vitesse, de précision ou de flexibilité, la bonne configuration fait une différence tangible.
Voici quatre applications courantes et éprouvées où les palettiseurs robots apportent une réelle valeur ajoutée.
Palettisation de boîtes
Les boîtes sont l’un des articles les plus couramment manipulés dans les applications de palettisation. Les palettiseurs robots permettent d’éviter les piles non équilibrées, les dommages dus à la surcompression ou la répartition inégale du poids.
Les solutions de palettisation de boîtes efficaces comprennent :
- un outil de bout de bras (EOAT) qui s’adapte à une gamme de tailles et de poids de boîtes
- un logiciel permettant de créer des modèles personnalisés par article ou par méthode d’expédition
- un système de guidage par vision pour corriger les boîtes mal alignées sur le convoyeur
- une capacité d’empilage répétable qui empêche le basculement et améliore la qualité de l’emballage
Cette approche est prisée dans presque tous les secteurs, y compris les biens de consommation, l’alimentation et les boissons, ainsi que la fabrication à caractère général, en particulier lorsque les traitements mixtes ou par lots sont fréquents.
Palettisation de sacs
Les produits ensachés nécessitent souvent plus qu’un simple empilage. Dans de nombreux secteurs industriels, les sacs doivent être équarris, aplatis ou étiquetés avant d’être mis sur palette. L’empilage manuel peut donner lieu à de l’instabilité, à une formation non homogène des couches, voire à une détérioration du produit.
Les systèmes robotisés permettent de remédier à ce problème grâce à :
- des dispositifs de mise à l’équerre permettant de maintenir les sacs alignés de manière à obtenir des couches propres
- des aplatisseurs intégrés permettant d’éliminer l’air emprisonné ou les gonflements
- des systèmes d’étiquetage qui appliquent des codes-barres ou des informations de suivi en cours de processus
- des outils de bout de bras (EOAT) conçus pour manipuler en douceur des charges souples ou en mouvement
Ces systèmes sont largement utilisés dans les lignes d’emballage d’aliments pour animaux, de farine, de graines et de produits agricoles. Il en résulte des palettes plus denses et plus stables qui résistent mieux au stockage et au transport.
Palettes de produits mixtes
La palettisation de charges mixtes est de plus en plus courante dans les centres de distribution et les opérations de commerce électronique. Les palettes peuvent alors contenir plusieurs UGS, dont la taille, la forme ou le poids varient souvent.
Les palettiseurs robots permettent d’obtenir un tel résultat grâce à :
- des systèmes de prélèvement guidés par vision conçus pour identifier et manipuler différents produits
- un logiciel qui élabore des modèles propres à la couche pour assurer l’équilibre et la stabilité
- des outils de bout de bras (EOAT) qui peuvent ajuster la prise ou l’orientation entre les prélèvements
Ce type de flexibilité permet de réduire les erreurs d’expédition, d’optimiser la densité des palettes et de répondre plus rapidement aux demandes d’emballage propres aux clients.
Il est particulièrement utile pour la logistique des aliments et des boissons, la logistique de tierce partie (3PL) et les opérations d’exécution des commandes en entrepôt.
Opérations à grande vitesse concernant les boissons
Les fabricants de boissons travaillent vite. Les solutions de palettisation dans ce domaine doivent suivre leur rythme sans sacrifier la qualité de la charge ou la disponibilité.
Dans les chaînes à vitesse soutenue, les palettiseurs robots sont souvent configurés pour traiter :
- 2 500 à 4 000 caisses par heure
- la formation de couches ou l’empilage par rangées
- les cartons à enveloppement, les plateaux ou les emballages sous film rétractable
- l’insertion des feuilles de palettisation pour garantir la stabilité du produit
- les convoyeurs de sortie intégrés menant aux machines d’emballage sous film étirable ou au stockage
L’objectif consiste à obtenir un débit maximal avec un minimum de points de contact. Moyennant une configuration appropriée de l’outil de bout de bras (EOAT) et du convoyeur, les robots peuvent maintenir leur vitesse et leur précision sur de longues périodes de travail, tout en réduisant la charge physique des employés.
Matériaux dangereux ou fragiles
Certains produits doivent être manipulés avec précaution en raison des risques de sécurité ou des dommages potentiels. Les produits en question peuvent inclure :
- les produits chimiques ou les poudres industrielles
- les contenants fragiles comme les bouteilles et les bocaux en verre
- les pièces métalliques lourdes ou de forme particulière
- les batteries, les fûts ou les sacs de matériaux en vrac
Les palettiseurs robots conçus pour ce type d’application comprennent souvent :
- des pinces personnalisées qui soutiennent l’article par le bas, enveloppent le produit ou utilisent le vide sans endommager les surfaces
- des outils de bout de bras (EOAT) dont le matériau est renforcé pour les objets lourds ou abrasifs
- une logique de palettisation qui permet d’éviter le chevauchement des produits ou les points de pression
- des enveloppes de protection lorsque la poussière, les fumées ou la température sont des facteurs à prendre en compte
Ces configurations sont courantes dans des secteurs comme l’industrie pharmaceutique, celle des produits chimiques spéciaux, l’électronique et la métallurgie, où la sécurité et la précision ne sont pas négociables.
Options de personnalisation du palettiseur robotisé
Il n’y a pas deux lignes de production identiques, c’est pourquoi les palettiseurs robots nécessitent souvent un certain degré de personnalisation. Cela dit, il n’est pas nécessaire de repartir depuis zéro pour tous les projets.
Solution sur mesure
Les systèmes de palettisation sur mesure sont construits à partir de zéro pour répondre aux exigences précises de la production. S’ils offrent une flexibilité maximale, ils s’accompagnent également de délais de livraison plus longs, de coûts initiaux plus élevés et d’une plus grande implication des ingénieurs.
Ce degré de personnalisation est le mieux adapté aux opérations impliquant :
- des besoins en matière de manutention de produits complexes
- des modèles de palettes ou des configurations de couches inhabituels
- une intégration étroite avec automatisation en amont ou en aval
- des environnements difficiles ou spécifiques (comme les entrepôts frigorifiques ou les zones très poussiéreuses)
- des objectifs à haut rendement avec peu de marge d’erreur
Ces projets supposent souvent des cadres sur mesure, de l’outillage, un concept d’agencement et l’intégration logicielle afin de garantir que le système fonctionne exactement comme il le faut.
Solutions standardisées
Il n’est pas nécessaire de partir de zéro pour tous les projets d’automatisation. Les systèmes de palettisation standardisés offrent aux fabricants une solution intermédiaire pratique, qui combine flexibilité et prévisibilité. Ces solutions sont conçues pour un déploiement plus rapide, une formation plus facile et un rendement fiable répondant aux besoins communs de fin de chaîne.
Plutôt que de se caractériser par de longs cycles de conception ou des coûts d’intégration élevés, les systèmes standardisés sont souvent préconfigurés avec du matériel, des logiciels et des dispositifs de sécurité compatibles, ce qui réduit au minimum le temps d’installation en plus d’atténuer la complexité à long terme.
TOMAMC est un exemple de cette approche
Élaboré par Premier Tech, le palettiseur Série PAL de TOMAMC est une solution de palettisation standardisée conçue en tenant compte de la facilité d’utilisation et d’un déploiement rapide. Son interface intuitive MOVNMC permet aux opérateurs de créer des configurations de palettes sans codage, tandis que les composants intégrés permettent de procéder à une installation rapide et à un élargissement modulaire en cas de besoin.
Pour les fabricants confrontés à des contraintes de main-d’œuvre, à un espace au sol limité ou à des environnements de production à forte mixité, les systèmes standardisés comme TOMAMC offrent une solution de départ plus accessible axée sur l’automatisation sans sacrifier le rendement ou la fiabilité.
Améliorations modulaires à valeur ajoutée
Il n’est pas nécessaire de s’engager dans un projet global dès le départ. Certains systèmes vous permettent d’ajouter des fonctionnalités en fonction de l’évolution de vos besoins. Les améliorations modulaires comprennent :
- Distributeurs de feuilles de palettisation pour une meilleure stabilité de la charge
- Distributeurs de palettes pour automatiser les permutations et réduire les temps d’arrêt
- Intégration d’une station d’emballage pour simplifier l’emballage en fin de chaîne
- Entrées à double convoyeur pour assurer une palettisation sur deux chaînes dans le même espace
Ces composants peuvent souvent être ajoutés ultérieurement dans le cas où vous optez pour une plateforme qui permet une croissance modulaire du système.
Combien coûte un palettiseur robotisé ?
Les palettiseurs robotisés constituent un investissement à long terme, et leur prix varie considérablement en fonction de l’application, de la vitesse requise et de la complexité du système. Voici une répartition générale fondée sur les scénarios d’utilisation les plus courants :
Type de système | Fourchette de prix (dollars US) |
---|---|
Palettiseurs robots standard | 130 000 $ à 250 000 $ |
Palettiseurs robots conçus sur mesure | 175 000 $ à 1 000 000 $ |
Le coût total peut également varier en fonction de ce qui suit :
- Exigences en matière de charge utile et de portée
- Type d’outil de bout de bras (EOAT) (p. ex. pince vs. ventouse)
- Utilisation de distributeurs de feuilles de palettisation ou de palettes
- Dispositif de vision et logiciel
- Complexité des permutations de produits
Les systèmes dotés d’une flexibilité intégrée ou d’options normalisées, comme ceux offerts par Premier Tech, peuvent réduire les délais d’ingénierie et aider à accélérer le déploiement, ce qui permet d’améliorer votre retour sur investissement plus rapidement.
Éléments à prendre en compte avant d’acheter
Avant d’installer un palettiseur robot, il est important de regarder au-delà des spécifications et d’étudier comment le système s’intègre dans votre environnement réel.
Exigences en matière d’espace
Les cellules robotisées traditionnelles nécessitent souvent plus d’espace en raison des clôtures, des tampons de sécurité et de l’équipement de soutien.
Si vous travaillez dans un espace restreint, les systèmes compatibles avec les cobots constituent une solution de rechange plus compacte. Leurs caractéristiques de sécurité réduisent la nécessité d’une grande zone de protection, ce qui permet de les intégrer plus facilement dans les zones de production restreintes.
Complexité de l’intégration
Certains systèmes sont plus faciles à mettre en place que d’autres. Les facteurs qui contribuent à faire augmenter la complexité de l’intégration sont les suivants :
- Nombre d’UGS ou de formats de produits
- Besoin de palettisation à charges mixtes ou de permutations fréquentes
- Coordination en amont et en aval avec les convoyeurs, les emballeuses ou les étiqueteuses
- Modèles de palettes sur mesure ou spécifications d’emballage strictes
Les plateformes normalisées peuvent réduire considérablement le temps d’intégration. Elles permettent également d’éviter des mises à niveau futures moins perturbatrices grâce à l’utilisation de modules préconfigurés.
Planifier l’avenir
Si vous achetez un robot dans le cadre d’un projet ponctuel seulement, vous risquez de vous heurter rapidement à des limites d’utilisation. Une stratégie plus judicieuse consiste à faire correspondre vos besoins actuels avec un système évolutif.
Posez-vous les questions suivantes :
- Le robot peut-il atteindre plusieurs positions de palettes ?
- Le logiciel sera-t-il capable de gérer de nouvelles UGS ultérieurement ?
- Serez-vous amené à intensifier votre production l’année prochaine ?
- Pourrez-vous ajouter des modules tels que des convoyeurs supplémentaires ou des outils propres à un modèle à l’avenir ?
En choisissant les critères de base dès maintenant, il sera plus facile de s’adapter sans avoir à tout recommencer plus tard.
Pourquoi un système de palettiseur robotisé vaut-il l’investissement ?
Les palettiseurs robots sont conçus pour remédier à certains des goulets d’étranglement les plus persistants dans les opérations de fin de ligne. En automatisant l’empilage manuel répétitif, ils réduisent les efforts physiques des travailleurs, améliorent la sécurité des opérateurs et garantissent une formation uniforme de la charge, réduisant ainsi au minimum les dommages causés aux produits pendant le stockage et le transport.
Pour ce qui concerne les entreprises confrontées à des pénuries de main-d’œuvre, à une augmentation de la demande ou à la variabilité des emballages, un système de palettisation robotisé offre un débit constant et libère des ressources humaines pour des tâches à plus forte valeur ajoutée. Il offre également une évolutivité à long terme sans les frais généraux liés à l’augmentation de votre effectif.
Grâce à des plateformes normalisées comme le palettiseur PAL-0830 de TOMAMC – système développé par Premier Tech – le déploiement est plus rapide, l’intégration est plus harmonieuse et le soutien continu est intégré. Ces systèmes offrent une voie simplifiée vers l’automatisation sans la complexité des solutions sur mesure.
Si vous envisagez d’apporter des améliorations en fin de ligne, notre équipe peut vous aider à déterminer si un palettiseur robot convient à vos produits, à l’agencement de vos installations et à vos objectifs de production.
Voyons un peu comment TOMAMC peut appuyer votre feuille de route en matière d’automatisation
FAQ concernant les palettiseurs robotisés
Qu’est-ce qu’un palettiseur robotisé ?
Un palettiseur robotisé est une machine qui empile automatiquement des produits - comme des boîtes, des sacs ou des seaux – sur une palette à l’aide d’un bras robotisé et de pinces spécialisées.
Quels sont les avantages des palettiseurs robotisés ?
Ils réduisent le travail manuel, améliorent la cohérence de l’empilage et libèrent des travailleurs pour des tâches plus qualifiées. Ils augmentent également le rendement et réduisent les accidents du travail.
Combien coûte un palettiseur robotisé ?
Les prix varient généralement entre 130 000 $ et 1 000 000 $ selon le type de produit, la vitesse requise et la complexité du système.
Quelle est la différence entre un palettiseur robot et un palettiseur conventionnel ?
Les palettiseurs conventionnels mettent en œuvre un mouvement mécanique déterminé pour former les couches. Les palettiseurs robots utilisent un bras programmable et un outil de bout de bras (EOAT) pour plus de flexibilité et de personnalisation.
Quelles industries utilisent un palettiseur robotisé ?
Les secteurs les plus courants sont l’alimentation et les boissons, l’agriculture, les produits pharmaceutiques, les aliments pour animaux de compagnie, l’industrie manufacturière et la distribution du commerce électronique.
Quelle est la cadence de travail d’un palettiseur robotisé ?
Les vitesses typiques vont de 14 à 80 produits par minute, en fonction du produit, de la pince et de la configuration du système.
Les palettiseurs robotiques sont-ils sécuritaires à utiliser autour des travailleurs ?
Oui. Les systèmes peuvent inclure des clôtures de sécurité, des détecteurs de zone ou utiliser des bras robots collaboratifs conçus pour fonctionner en toute sécurité à proximité des personnes.
Le potentiel des cobots vous intéresse ?
Découvrez TOMAMC, la toute dernière innovation de Premier Tech, conçue pour rendre l'automatisation friendustrialMC. Visitez notre page dédiée au palettiseur TOMAMC pour en savoir plus.