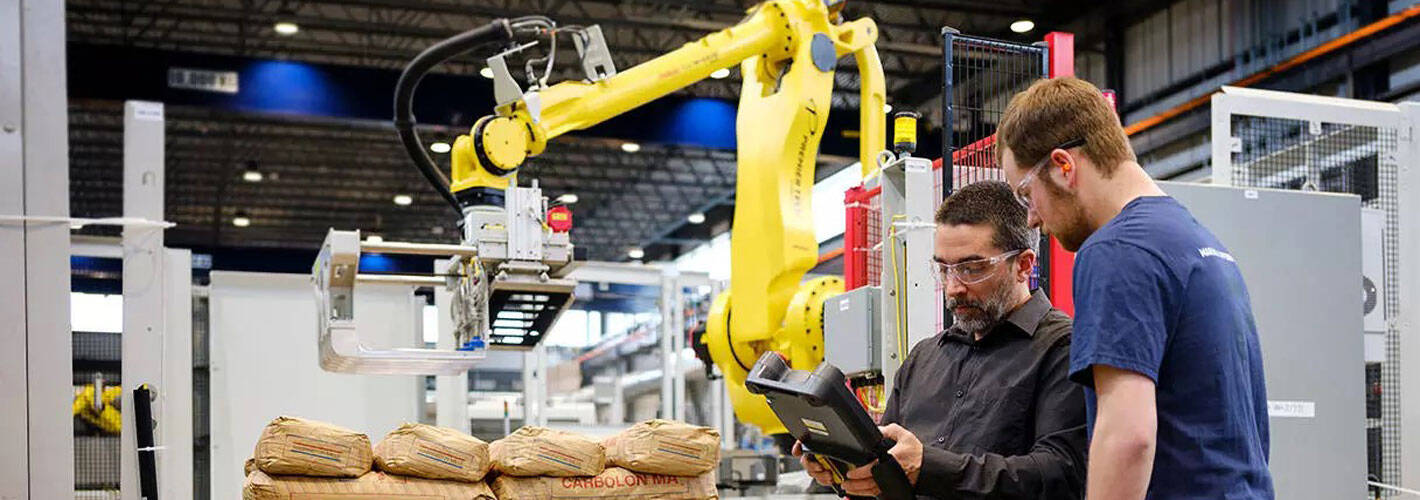
Before you invest in a palletizing robot: read this guide first
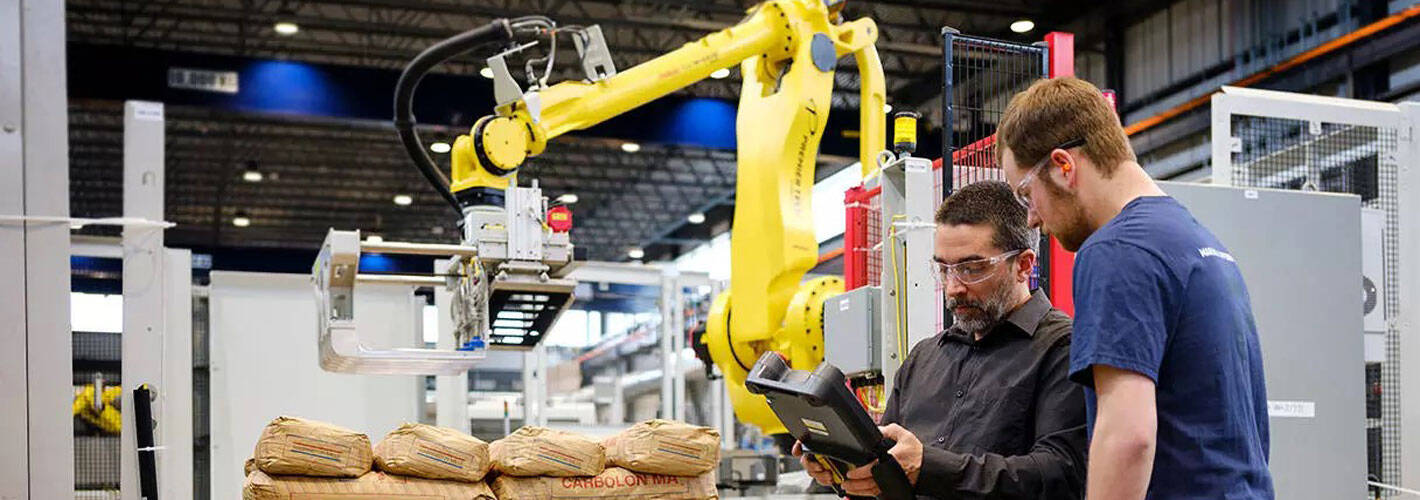
Not all palletizing robots are built the same, and picking the right one requires more than comparing payload specs or price tags.
Some systems are plug-and-play. Others require heavy engineering. Some fit into smaller spaces, while others take up half your floor.
This guide breaks down everything you need to know, from system types and real-world use cases to integration, safety, and cost. Whether you are automating for the first time or expanding what is already in place, this will help you figure out what fits, what doesn’t, and why.
Let’s make sure you’re asking the right questions before you invest in a palletizing robot.
What is a palletizing robot?
A palletizing robot uses a robotic arm to stack products onto a pallet. It can pick up items one at a time, in rows, or full layers depending on the tool attached to the arm. Some systems also include vision technology, which helps the robot place items more precisely, even overlapping bags when needed.
Do you need a palletizing robot? (And when you don’t)
Investing in robotic palletizing can deliver major results. But it’s not always the right move for every facility. Some operations just aren’t ready for automation yet and pushing it too early can create more problems than it solves.
A quick fit check
Ask yourself these questions to see if robotic palletizing makes sense for your operation:
- Are we consistently falling behind on palletizing?
- Do we struggle to staff palletizing roles, especially for evening or weekend shifts?
- Have we recorded injuries or complaints tied to repetitive lifting or awkward stacking tasks?
- Do we need to increase throughput without adding more headcount?
- Do inconsistent pallets or poor stacking lead to rejected loads or shipping issues?
- Would moving workers off repetitive palletizing free them up for more skilled or flexible roles?
If you answered “yes” to most of those, your operation is likely a strong candidate for robotic palletizing.
Advantages and disadvantages
Like any tool, robotic palletizers have pros and cons. Here is a quick breakdown to help you weigh the decision.
Advantages of robotic palletizers
- Consistent load quality and stacking accuracy across shifts and SKUs
- Reduces ergonomic risks from repetitive lifting and heavy load handling
- Frees up skilled labor for higher-value tasks like equipment setup or QA
- Scalable throughput to match seasonal or long-term production growth
- Can operate in lights-out shifts or during labor gaps without supervision
- May qualify for government or industry grants tied to safety or productivity gains
Considerations and limitations of palletizing robots
- Upfront capital cost and lead time for procurement and installation
- Potential need for layout rework to accommodate robot reach, guarding, or flow
- Training required for operators and maintenance personnel to manage the system
- Less suited for low-volume SKUs or highly variable/unpredictable load configurations
The type of palletizing system you choose can have a big impact on how complex or time-consuming your project becomes. It’s worth understanding the different system types so you can choose one that fits your timeline, resources, and goals.
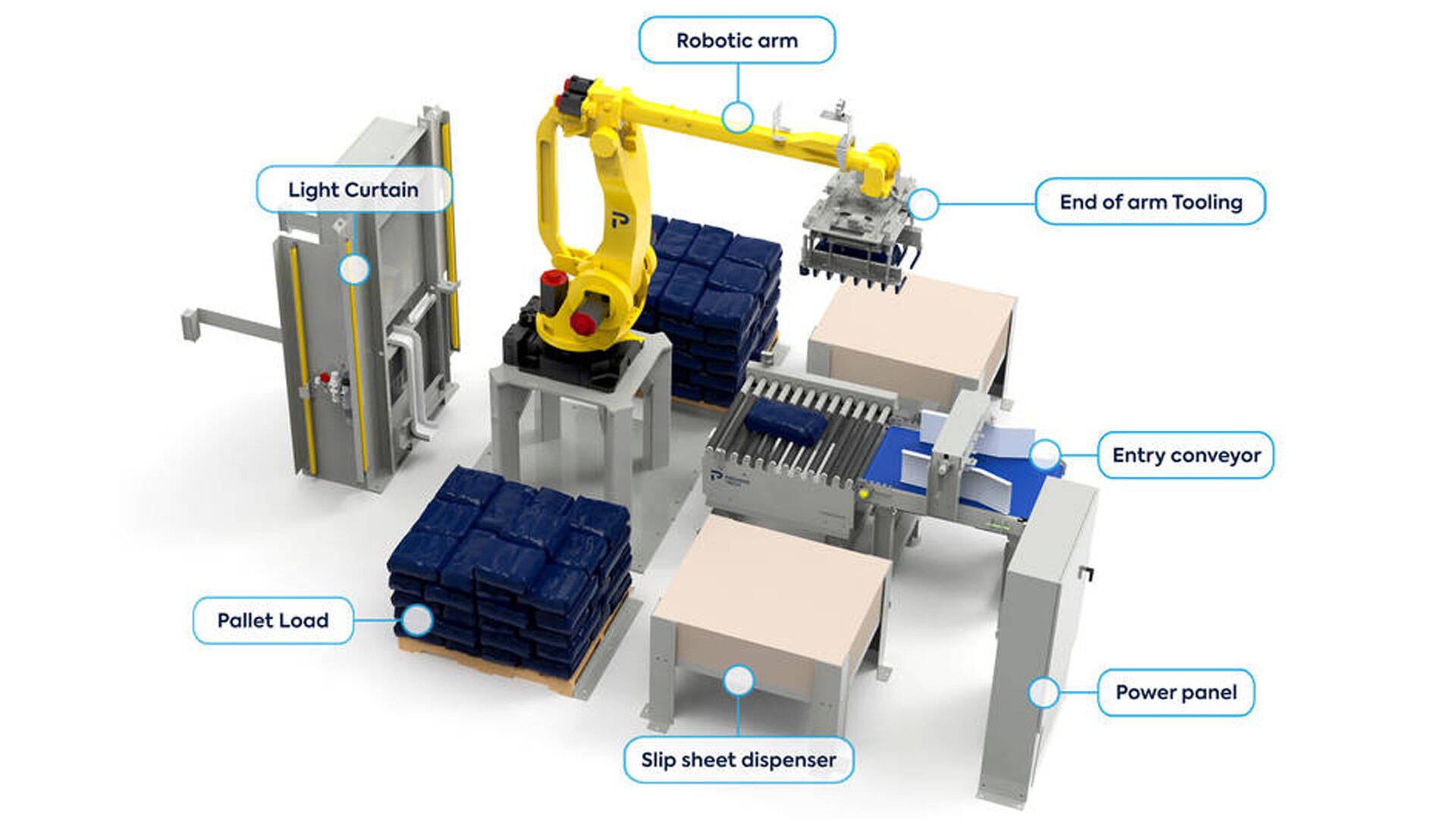
Types of palletizing robots
Robotic palletizers come in a range of configurations, from basic setups to fully automatic systems built for nonstop production. The right one for you will depend on your volume, footprint, and how much manual handling you want to eliminate.
Basic robotic systems
These are the simplest forms of robotic palletizers. They give you the benefits of automation without the complexity or cost of a fully integrated system.
A basic system typically includes:
- A robotic arm
- End-of-arm tooling
- An infeed conveyor
- Safety fencing or area scanners
What’s missing is automation beyond the stacking process. There’s no pallet dispenser or slip sheet dispenser.
The pallet usually sits on the floor and must be removed by forklift or hand truck. Every time a pallet is full, the system pauses until someone places an empty pallet.
Basic systems can reduce manual lifting and improve stack consistency, but they still rely on operators for regular intervention.
Fully automatic robotic systems
These systems are built for continuous operation with little to no manual involvement. They can palletize at high speeds, handle various product types, and run through shift changes without missing a beat.
A fully automatic setup includes:
- A robotic arm
- End-of-arm tooling
- An infeed conveyor
- A pallet dispenser
- A slip sheet dispenser
- Safety fencing or area scanners
- An exit conveyor that moves full pallets to a wrap station or handoff zone
Here’s how it works:
Products move in on the entry conveyor. The pallet dispenser loads an empty pallet into position. A slip sheet may be placed first. Then the robot begins stacking items, row by row or layer by layer. Once complete, the full pallet is transferred out, and the process repeats automatically.
One key benefit is that you can refill the pallet magazine without stopping the system. That alone can save hours of downtime over the course of a week.
Robotic palletizer technologies
Not all robotic palletizers use the same kind of robot arm. The two main options are traditional industrial robots and collaborative robots (cobots). Each comes with its own tradeoffs and is better suited to different environments.
Traditional robot arms are faster, support heavier payloads, and are typically used in high-throughput, fully automatic systems. These require safety fencing or light curtains and more physical space.
Cobots are designed to work safely alongside people, with built-in safety features like force and speed limitations. They don’t require full guarding, which makes them ideal for compact work areas or operations where humans need to interact closely with the cell.
Collaborative technology is especially helpful in plants with limited floor space or evolving production needs.
What to look for in a palletizing robot
A robotic palletizer is only as good as its individual components. Choosing the right one means knowing what to pay attention to, starting with the arm and ending with the way your team interacts with the software.
The arm: payload, reach, and control
Every palletizing robot starts with the arm. The two most common types are traditional industrial robots and collaborative robots, or cobots.
Industrial robot arms can lift heavier payloads and move faster. They are great for high-throughput environments but typically require more space and safety guarding.
Cobots are built to work safely around people. They offer lower payload capacity and slower speeds but take up less room and can often run without fencing.
When comparing arms, look at these specs:
- Payload capacity: How much weight the arm can lift per pick.
- Reach: How far the arm can extend from its base.
- Axis control: The number of joints and how they help position or rotate the load.
These specs determine what types of products you can handle, how fast you can move them, and whether the robot can reach across one or multiple pallet positions.
The end-of-arm tooling (EOAT)
The gripper does the real work. Your end-of-arm tooling determines what the robot can lift, how reliably it places items, and whether it can adapt to different product shapes or materials.
Here are common types and what they are used for:
- Clamp gripper: Uses metal plates to squeeze either side of a bag or box for lifting. Ideal for rigid or packed products.
- Finger gripper: Slips tines under the sides of a product. Often used for bags of different sizes and materials.
- Fork gripper: Lifts open-top boxes or large bags from the bottom. Great for oversized or unstable items.
- Magnetic gripper: Picks up metal parts like cans or construction materials without damaging them.
- Pail gripper: Designed specifically to lift plastic or metal pails by gripping just below the lid.
- Ring gripper: Lifts drums or large round containers from the top using a circular attachment.
- Slip Sheet gripper: A handy add-on that allows the robot to place slip sheets or pallets in addition to products.
- Vacuum gripper: Uses suction to lift items gently from the top. Useful for fragile or lightweight products.
The right gripper depends on what you are palletizing, how delicate it is, and how varied your product catalog is.
Robotic palletizer software
The robot is the muscle. The software is the brain.
Look for palletizing software that simplifies pattern building, not one that adds complexity. Drag-and-drop interfaces, visual editors, and AI-based adjustments can help your team set up and update programs without needing to code.
If you are running multiple SKUs or need to switch pallet patterns often, make sure the software makes that easy too.
Vision systems for palletizing robots
In palletizing applications, vision systems support accuracy, flexibility, and consistent uptime, especially in dynamic production environments.
Integrated vision allows the robot to locate, identify, and orient products in real-time. This is valuable when handling:
- Inconsistent product presentation at the infeed, such as variable spacing or orientation
- Soft or deformable packaging, including shrink-wrapped trays or polybags
- Mixed-SKU pallets, where the robot must differentiate and place multiple case types accurately
Vision enables the system to adjust dynamically to product variations, reducing the need for physical rework or line stoppages. It supports:
- Corrective alignment in real time
- Faster cycle times by eliminating delays from misfeeds
- Fewer operator interventions, especially when SKUs change frequently
Vision-equipped palletizers maintain performance even with variability on the line, helping operations stay efficient without over-engineering mechanical controls.
Safety: fencing, scanners, and layout considerations
Safety isn’t just about meeting regulations. It also affects floor space and system design.
- Traditional robots usually need full guarding with fencing and interlocks.
- Cobots use built-in safety features like force and speed limitations to operate in shared spaces.
- Light curtains and area scanners are often used with both robots and cobots to further protect people nearby without boxing off the cell.
The safer your system is by design, the less disruption it creates on your floor. If you are working in a tight or high-traffic area, this makes a big difference.
Safety: cell design, risk assessment, and functional zoning
Palletizing automation requires thoughtful safety design that balances operator protection, efficient workflow, and space optimization.
Traditional industrial robots typically operate within fully enclosed safety cells equipped with interlocked fencing, safety-rated doors, and emergency stop devices to meet Performance Level (PL) requirements.
Collaborative palletizers integrate power and force limiting (PFL) features, allowing operation in proximity to personnel. However, a task-specific risk assessment is still required to determine the appropriate level of protection for the entire application, not just the robot arm.
Modern systems often include area scanners, light curtains, or safety mats to define functional safety zones that restrict access during motion while maintaining line-of-sight and minimizing space usage. This is especially valuable in end-of-line environments where floor space is constrained or traffic flow is high.
A well-engineered safety architecture ensures compliance with ISO 10218 and TS 15066 standards while supporting fast commissioning, efficient layout design, and long-term usability on the production floor.
Application use cases for palletizing robots
Robotic palletizers can handle a wide range of tasks, but the best systems are built around very specific goals. Whether it’s speed, precision, or flexibility, the right configuration makes a measurable difference.
Here are four common and proven applications where robotic palletizers add real value.
Box palletizing
Boxes are one of the most common items handled in palletizing applications. Robotic palletizers help avoid skewed stacks, damage from over-compression, or uneven weight distribution.
Effective box palletizing solutions feature:
- EOAT that accommodates a range of box sizes and weights
- Software for building custom patterns by SKU or shipping method
- Vision guidance to correct misaligned boxes on the conveyor
- Repeatable stacking that prevents toppling and improves wrap quality
This approach is popular across nearly every industry, including consumer goods, food and beverage, and general manufacturing, especially where mixed or batch runs are frequent.
Bag palletizing
Bagged products often require more than just stacking. In many industries, bags must be squared, flattened, or labeled before they are palletized. Manual stacking can lead to instability, inconsistent layer formation, and even product damage.
Robotic systems solve this with:
- Squaring devices to keep bags aligned for clean layers
- Integrated flatteners to remove trapped air or bulges
- Labeling systems that apply barcodes or tracking info mid-process
- End-of-arm tooling designed to handle soft or shifting loads gently
This setup is widely used in pet food, flour, seed, and agricultural packaging lines. It results in denser, more stable pallets that hold up better in storage and transit.
Mixed product pallets
Mixed-load palletizing, often called "rainbow palletizing," is increasingly common in distribution centers and eCommerce operations. These pallets may include several SKUs, often varying in size, shape, or weight.
Robotic palletizers make this possible with:
- Vision-guided pick systems to identify and handle different products
- Software that builds layer-specific patterns for balance and stability
- EOAT that can adjust grip or orientation between picks
This kind of flexibility helps reduce shipping errors, optimize pallet density, and respond faster to customer-specific packing requests.
It is particularly valuable in food and beverage logistics, third-party logistics (3PL), and warehouse fulfillment operations.
High-speed beverage operations
Beverage manufacturers run fast. Palletizing solutions in this space must match that pace without sacrificing load quality or uptime.
In high-speed lines, robotic palletizers are often configured to handle:
- 2,500 to 4,000 cases per hour
- Layer forming or row-based stacking
- Wrap-around cartons, shrink-wrapped packs, or trays
- Slip sheet insertion for product stability
- Integrated outfeed conveyors leading to stretch wrappers or storage
The goal here is maximum throughput with minimal touchpoints. With the right EOAT and conveyor setup, robots can maintain speed and accuracy over long shifts while reducing the physical burden on workers.
Hazardous or delicate materials
Some products require careful handling due to safety risks or the potential for damage. These may include:
- Chemicals or industrial powders
- Fragile containers such as glass bottles or jars
- Heavy or oddly shaped metal parts
- Batteries, drums, or bulk material bags
Robotic palletizers designed for this type of application often include:
- Custom grippers that support from the bottom, wrap around the product, or use vacuum without damaging surfaces
- Reinforced EOAT materials for heavy or abrasive items
- Palletizing logic that avoids product overlap or pressure points
- Environmental enclosures if dust, fumes, or temperature are factors
These configurations are common in industries like pharmaceuticals, specialty chemicals, electronics, and metal manufacturing, where safety and precision are non-negotiable.
Palletizing robot customization options
No two production lines are the same, which is why robotic palletizers often require some level of customization. That said, not every project needs to start from scratch.
Custom engineered solution
Custom-engineered palletizing systems are built from the ground up to meet exact production requirements. While they offer maximum flexibility, they also come with longer lead times, higher upfront costs, and more engineering involvement.
This level of customization is best suited for operations with:
- Complex product handling needs
- Unusual pallet patterns or layer configurations
- Tight integration with upstream or downstream automation
- Harsh or specialized environments (like cold storage or high-dust areas)
- High throughput goals with little room for error
These projects often involve custom frames, tooling, layout design, and software integration to ensure the system performs exactly as needed.
Standardized solutions
Not every automation project needs to start from scratch. Standardized palletizing systems offer manufacturers a practical middle ground, balancing flexibility with predictability. These solutions are pre-engineered for faster deployment, easier training, and reliable performance across common end-of-line needs.
Instead of lengthy design cycles or high integration costs, standardized systems often come pre-configured with compatible hardware, software, and safety features, minimizing setup time and reducing long-term complexity.
TOMA™ is one example of this approach
Developed by Premier Tech, the TOMA™ PAL Series palletizer is a standardized palletizing solution designed around ease of use and rapid deployment. Its MOVN™ HMI interface lets operators create pallet configurations without coding, while integrated components support quick installation and modular expansion when needed.
For manufacturers dealing with labor constraints, limited floor space, or high-mix production environments, standardized systems like TOMA™ offer a more accessible entry point to automation, without sacrificing performance or reliability.
Modular upgrades that add value
You don’t need to commit to everything up front. Some systems allow you to expand functionality as your needs evolve. Modular upgrades include:
- Slip sheet dispensers for better load stability
- Pallet dispensers to automate changeovers and reduce downtime
- Wrap station integration to streamline end-of-line packaging
- Dual-conveyor inputs for two-line palletizing within the same footprint
These components can often be added later if you choose a platform that supports modular growth.
How much does a palletizing robot cost?
Palletizing robots are a long-term investment, and pricing varies widely depending on your application, speed requirements, and system complexity. Below is a general breakdown based on common use cases:
System Type | Cost Range (USD) |
---|---|
Standard Robotic Palletizer | $130,000 to $250,000 |
Custom Engineered Robotic Palletizer | $175,000 to $1,000,000 |
The total cost may also vary depending on:
- Payload and reach requirements
- Type of EOAT (e.g., clamp vs. vacuum)
- Use of slip sheet or pallet dispensers
- Vision and software features
- Complexity of product changeovers
Systems with built-in flexibility or standardized options, like those offered by Premier Tech, may reduce engineering time and help speed up deployment, improving your return on investment sooner.
Considerations to think about before buying
Before installing a robotic palletizer, it's important to look beyond the specs and consider how the system fits into your actual environment.
Space requirements
Traditional robot cells often require more space because of fencing, safety buffers, and support equipment.
If you are working with limited room, cobot-enabled systems offer a more compact alternative. Their built-in safety features reduce the need for hard guarding, making them easier to fit into tight production areas.
Integration complexity
Some systems are easier to drop into place than others. Factors that increase integration complexity include:
- Number of SKUs or product formats
- Need for mixed-load palletizing or frequent changeovers
- Upstream and downstream coordination with conveyors, wrappers, or labelers
- Custom pallet patterns or tight wrapping specs
Standardized platforms can significantly reduce integration time. They also make future upgrades less disruptive by using pre-configured modules.
Plan for the future
If you are buying for today only, you may hit limits fast. A better approach is to match your current needs with a system that can scale.
Consider:
- Can the robot reach multiple pallet positions?
- Is the software capable of handling new SKUs later on?
- Will you need to increase throughput next year?
- Can you add modules like extra conveyors or pattern tools down the road?
Choosing the right foundation now makes it easier to adapt without starting over later.
Why a palletizing robot system is worth the investment
Robotic palletizers are designed to solve some of the most persistent bottlenecks in end-of-line operations. By automating repetitive manual stacking, they reduce physical strain on workers, improve operator safety, and ensure uniform load formation, minimizing product damage during storage and transit.
For operations navigating labor shortages, increasing demand, or variability in packaging, a robotic palletizing system delivers consistent throughput and frees up human resources for higher-value tasks. It also brings long-term scalability without the overhead of growing your workforce.
With standardized platforms like TOMA™ PAL Series palletizer, developed by Premier Tech, deployment is faster, integration is smoother, and ongoing support is built in. These systems offer a streamlined path to automation without the complexity of custom-engineered solutions.
If you’re evaluating end-of-line improvements, our team can help assess whether a robotic palletizer is the right fit for your products, facility layout, and production goals.
Let’s talk about how TOMA™ can support your automation roadmap
Palletizing Robot FAQ
What is a robotic palletizer?
A robotic palletizer is a machine that automatically stacks products—such as boxes, bags, or pails—onto a pallet using a robotic arm and specialized grippers.
What are the advantages of robotic palletizers?
They reduce manual labor, improve stacking consistency, and free up workers for more skilled roles. They also increase throughput and reduce workplace injuries.
How much does a robotic palletizer cost?
Prices typically range from $130,000 to $1,000,000, depending on product type, speed requirements, and system complexity.
What is the difference between a robotic and conventional palletizer?
Conventional palletizers use fixed mechanical movement to form layers. Robotic palletizers use a programmable arm and EOAT for more flexibility and customization.
What industries use robotic palletizers?
Common industries include food and beverage, agriculture, pharmaceuticals, pet food, manufacturing, and eCommerce distribution.
How fast is a robotic palletizer?
Typical speeds range from 14 to 80 products per minute, depending on the product, gripper, and system configuration.
Are robotic palletizers safe to use around workers?
Yes. Systems may include safety fencing, area scanners, or use collaborative robot arms that are designed to operate safely near people.
Interested in the power of cobots?
Premier Tech’s latest offering, TOMA™, is all about making automation Friendustrial™. Head over to our TOMA™ Palletizer page to learn more.