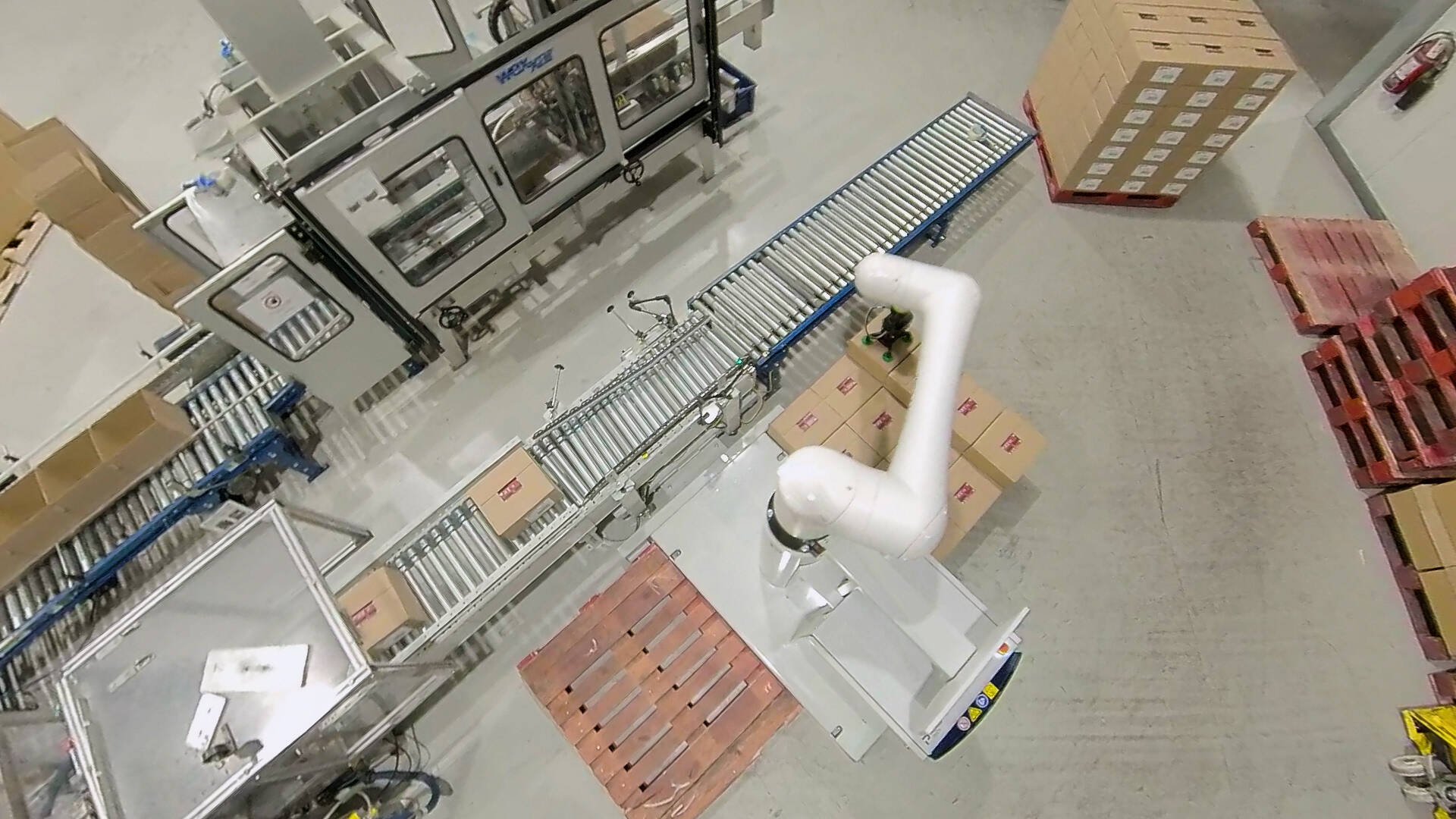
Combien coûte un palettiseur robotisé? Les facteurs qui influencent votre investissement
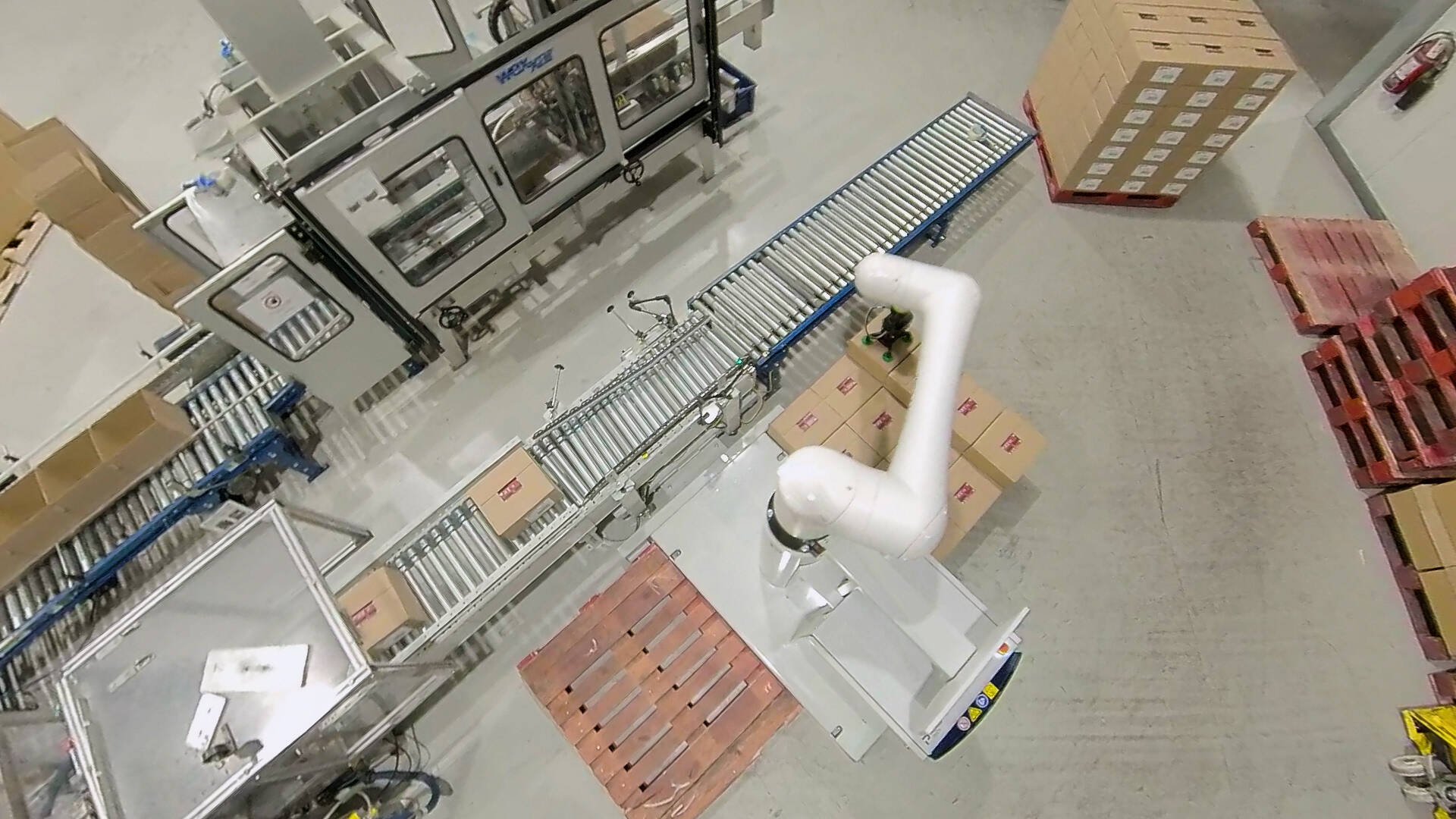
Découvrez le coût des palettiseurs robotisés, les principaux facteurs de prix et comment estimer le RSI pour choisir la solution de palettisation adaptée à votre installation.
Si vos opérations de fin de ligne ont du mal à suivre le rythme de production, la palettisation robotisée est probablement déjà sur votre radar.
Les palettiseurs robotisés automatisent les tâches répétitives en fin de ligne, améliorant la vitesse, la constance et la sécurité. Ils sont aussi assez flexibles pour évoluer avec vos besoins de production.
Alors que l’automatisation devient de plus en plus courante, une question revient souvent : quel est le coût d’un palettiseur robotisé?
La réponse dépend de plusieurs facteurs, notamment la conception du système, les besoins de production et la manière dont la solution s’intègre à votre flux de travail existant. Comprendre ces variables est essentiel pour faire un investissement intelligent.
Dans ce guide, nous allons examiner les fourchettes de prix typiques, les principaux facteurs de coût et la façon de déterminer si un palettiseur robotisé est adapté à votre réalité.
Combien coûte un système de palettisation?
Les prix des systèmes de palettisation varient considérablement en fonction du type de technologie utilisée, de la vitesse de production, du niveau d’automatisation et des exigences d’intégration. Voici un aperçu général des gammes de prix typiques :
- Système manuel ou semi-automatique : prix très variable, selon le niveau d’automatisation. Ce type de système repose fortement sur la main-d’œuvre.
- Système conventionnel : coûte généralement entre 275 000 $ et 1 000 000 $, selon la vitesse (BPM ou CPM), l’aménagement de l’usine et le type de produit.
- Système robotique (traditionnel ou collaboratif) : à partir d’environ 100 000 $ pour les unités collaboratives les plus simples, et jusqu’à 900 000 $ pour des bras robotisés à haute vitesse traitant des charges lourdes ou effectuant des mouvements complexes.
- Système hybride : prix très variable en fonction des besoins, mais pouvant atteindre plus d’un million de dollars.
Les prix peuvent changer considérablement en fonction du taux de production, du niveau d’automatisation et du niveau de personnalisation de votre opération. Ces montants servent de point de départ général, mais il faudra observer les besoins spécifiques de votre système pour avoir une estimation plus précise.
Pourquoi les palettiseurs collaboratifs sont un point d’entrée intelligent
Si vous cherchez une solution qui ne nécessite pas de repenser entièrement la disposition de votre usine, les palettiseurs collaboratifs (cobots) offrent une approche plus accessible de l’automatisation. Compacts, sécuritaires pour les employés travaillant à proximité et faciles à programmer, ils conviennent parfaitement aux installations qui amorcent leur transition vers la palettisation robotisée.
Le palettiseur TOMAMC utilise la technologie cobot dans une plateforme standardisée qui est rapide à déployer et facile à utiliser. Conçu autour de MOVNMC, l’interface intuitive la plus avancée du marché, il rend la palettisation plus accessible sans compromis sur la sécurité, la stabilité ou la performance.
Vous souhaitez savoir combien coûte un palettiseur collaboratif et quel sera son impact sur votre rentabilité?
Estimez votre retour sur investissement grâce au calculateur FriendustrialMC de RSI pour palettiseur collaboratif, et découvrez comment vos données de production influencent les coûts, la rentabilité et les économies à long terme.
Qu’est-ce qui influence le coût d’un système de palettisation?
De la vitesse de votre ligne de production à la disposition de votre usine, chaque détail aura une influence sur le coût du système.
1. Type de système
Le type de système de palettisation que vous choisissez joue un rôle majeur, à la fois en termes de coût et de valeur à long terme.
- Système manuel ou semi-automatique : coût initial le plus bas, mais repose fortement sur le travail manuel et offre une évolutivité limitée.
- Système conventionnel : conçu pour la vitesse et le volume. Ce grand système mécanique a un prix plus élevé en raison de sa complexité.
- Système robotique : comprend des bras industriels traditionnels ou des robots collaboratifs. Le prix varie selon la vitesse de cycle, la capacité de charge, les besoins en programmation et la flexibilité.
- Système hybride : solution sur mesure qui combine plusieurs technologies. C’est généralement le plus complexe et le plus difficile à chiffrer sans analyse détaillée.
Certains systèmes sont plus faciles à installer, nécessitent moins de formation et comprennent des commandes intuitives pour une utilisation quotidienne. Ces différences influent sur les besoins en main-d’œuvre, les coûts d’intégration et la maintenance, et elles ont un impact direct sur le retour sur investissement.
2. Vitesse de production
Des vitesses plus élevées nécessitent généralement des structures plus robustes, des actionneurs plus rapides et des contrôles plus avancés, ce qui augmente le coût global.
- Les palettiseurs conventionnels sont conçus pour les lignes à haut débit et peuvent traiter de grands volumes avec peu de variations. Ils sont généralement utilisés dans des usines avec des lignes à haut débit et des configurations répétitives.
- Les systèmes robotiques traditionnels permettent également des vitesses modérées à élevées et offrent une flexibilité quant aux types de produits et aux configurations de palettisation, tout en maintenant un rendement constant. Ils sont bien adaptés pour les entreprises qui gèrent un volume de production avec une certaine variabilité.
- Les robots collaboratifs sont idéaux pour les environnements à faible ou moyen débit. Moins rapides que les systèmes industriels, ils sont toutefois plus simples à utiliser, plus sécuritaires et plus adaptables – notamment lorsque les tailles des lots ou les cycles de production varient.
Les opérations à production continue et à grand volume doivent généralement faire face à des coûts initiaux plus élevés. Atteindre des performances à haute vitesse nécessite souvent des investissements supplémentaires en outillage, en convoyeurs et en intégration pour assurer l’alignement optimal du système.
3. Niveau d’automatisation
Le niveau d’automatisation de votre système de palettisation affecte à la fois son coût et sa complexité.
- Système semi-automatisé : les opérateurs participent encore à certaines tâches, comme le chargement manuel des produits ou la manipulation des palettes. Ce système est moins coûteux, mais dépend davantage de la main-d’œuvre.
- Système entièrement automatisé : gère la détection des produits, l’empilage et le changement de palettes sans intervention humaine. Il nécessite des contrôles avancés, des protocoles de sécurité et une intégration avec les équipements en amont et en aval.
Des niveaux d’automatisation plus élevés exigent souvent plus de temps de programmation et de configuration. Même si l’intervention des opérateurs diminue, une formation est nécessaire pour utiliser l’IHM, redémarrer le système et effectuer des ajustements mineurs. L’investissement initial est plus élevé, mais les coûts de main-d’œuvre à long terme peuvent être inférieurs.
4. Outillage du bras (pinces)
Les pinces sont l’un des composants les plus importants de tout système de palettisation. Le bon outillage dépend du type de produits que vous manipulez, de leur forme et de leur poids.
- Sacs : nécessitent souvent des préhenseurs mécaniques ou de type pinces pour bien contrôler le déplacement du poids.
- Caisses et boîtes : utilisent généralement des préhenseurs à vide ou à ventouses adaptés aux surfaces rigides et planes.
- Articles fragiles ou irréguliers : peuvent nécessiter un outillage personnalisé ou hybride pour éviter d’endommager le produit.
Plus un produit est spécialisé, plus les pinces nécessaires seront complexes et coûteuses. L’outillage affecte à la fois le prix initial du système et les coûts à long terme, en particulier si des changements de produits fréquents nécessitent des ajustements ou des remplacements.
5. Capteurs, vision et convoyeurs
Les capteurs et les convoyeurs sont des composants intégrés qui influencent considérablement l’efficacité et le coût d’un système de palettisation.
- Capteurs et vision : utilisés pour des tâches telles que la détection des boîtes, l’orientation et le contrôle de la qualité, les capteurs et les systèmes de vision garantissent un placement précis du produit et la fiabilité du système. Les configurations avancées peuvent détecter divers types d’emballages, y compris les articles brillants, foncés ou emballés avec du film étirable.
- Convoyeurs : responsables de l’acheminement des produits vers la bonne position pour la palettisation. La conception, la vitesse et la longueur du convoyeur influencent directement les coûts. Les fonctionnalités supplémentaires, comme les bras de déviation, les rouleaux motorisés ou les vannes tiroirs, peuvent augmenter le prix d’un système de convoyage de 10 000 $ à 50 000 $ ou plus, selon la configuration.
La qualité et la complexité des composants ont un impact direct sur les coûts d’intégration. Des capteurs de haute qualité et des convoyeurs bien conçus peuvent améliorer l’efficacité, mais ils augmenteront les dépenses initiales. À l’inverse, les composants bas de gamme peuvent coûter moins cher à l’achat, mais ils entraîneront souvent plus d’entretien et une fiabilité réduite au fil du temps.
6. Exigences d’intégration
L’intégration ajoute du temps, des coûts et de la complexité, en particulier lorsqu’un palettiseur doit se connecter à d’autres systèmes de votre ligne. Des convoyeurs et des emballeurs de caisses aux emballeuses, aux étiqueteuses et aux logiciels de gestion d’entrepôt, plus vous devez synchroniser d’équipements, plus la planification et l’ingénierie requises seront importantes.
- Connectivité du système : les palettiseurs doivent souvent s’interfacer avec des machines en amont ou en aval et peuvent avoir besoin de se connecter à des systèmes ERP ou à des contrôles au niveau de l’usine. Cela nécessite une compatibilité avec votre infrastructure numérique existante et peut impliquer des logiciels ou des intergiciels supplémentaires.
- Rétrofit dans les lignes existantes : certaines opérations peuvent réduire les coûts d’intégration en plaçant le palettiseur dans une station manuelle existante ou en utilisant les convoyeurs actuels. Les unités compactes ou modulaires sont généralement plus faciles à installer, nécessitant un minimum de modifications à l’aménagement de votre usine.
- Ingénierie sur mesure : plus l’intégration est personnalisée, plus il est probable que vous aurez besoin de programmation PLC, de mappage d’E/S et de synchronisation avec des systèmes existants. Cela augmentera à la fois le temps d’ingénierie et les coûts de mise en service.
C’est là que des solutions standardisées comme TOMAMC peuvent simplifier le processus. TOMAMC utilise la technologie cobot dans une plateforme préconçue visant à réduire la complexité de l’intégration. Avec ses outils intégrés, son interface IHM simplifiée et son format compact, elle est pensée pour un déploiement rapide et une mise en production accélérée.
En savoir plus sur le palettiseur collaboratif TOMAMC et la façon dont il peut accélérer votre processus de palettisation.
7. Entretien et maintenance
L’entretien continu fait partie du coût total de possession de tout système de palettisation. Cela comprend les inspections, le remplacement des pièces d’usure et l’assistance technique occasionnelle.
- Ce qui est inclus : les vérifications planifiées, les pièces d’usure de base (comme les ventouses ou les bandes de convoyeur), les remplacements de piles et les mises à jour logicielles.
- Coût annuel typique : pour la plupart des systèmes, le coût de la maintenance varie entre 3 et 10 % du prix d’achat. Par exemple, un palettiseur conventionnel au prix de 750 000 $ peut coûter de 22 500 $ à 75 000 $ par année.
Cependant, des solutions standardisées comme TOMAMC sont conçues pour un entretien minimal. En l’absence d’entretien du robot pendant 8 ans et grâce au nombre limité de pièces d’usure, les coûts annuels typiques restent souvent inférieurs à 2 000 $.
Demandez à votre fournisseur une estimation des coûts de maintenance en fonction de votre type de système et de l’usage que vous en ferez.
8. Coûts d’exploitation et frais généraux
Le coût total d’un système de palettisation va au-delà du prix d’achat. Les dépenses d’exploitation comme l’électricité, l’amortissement et la formation jouent un rôle dans votre retour sur investissement à long terme.
- Consommation électrique : les systèmes plus grands consomment plus d’énergie et peuvent coûter beaucoup plus cher en fonction de la durée d’exécution et de la charge.
- Amortissement : la plupart des palettiseurs peuvent être amortis jusqu’à une période de 10 ans, ce qui vous permet de récupérer une partie du coût grâce à des déductions fiscales, tout en tenant compte de l’investissement en capital.
Ces coûts opérationnels s’accumulent au fil du temps et doivent être pris en compte dans tout modèle de RSI ou de budgétisation précis.
Variables de coût supplémentaires à garder en tête
Au-delà des coûts liés au système et à son intégration, plusieurs dépenses souvent négligées peuvent influencer le montant total de votre investissement. Ces coûts n’apparaîtront pas nécessairement dans le devis, mais ils auront tout de même un impact sur votre rentabilité à long terme.
Coûts d’installation
Les coûts d’installation varient en fonction de la complexité du système, de l’emplacement de votre usine, de la présence ou non d’une équipe d’automatisation interne ainsi que du niveau d’intégration requis. Les systèmes nécessitant une programmation sur mesure, plusieurs points de connexion ou une adaptation à des espaces restreints prennent souvent plus de temps à installer et à mettre en service.
Certaines solutions de palettisation arrivent en plusieurs pièces et nécessitent du temps supplémentaire sur place pour l’assemblage mécanique et logiciel. En plus de prolonger le temps de mise en place, cela peut aussi retarder le démarrage de la production si vos ressources internes sont limitées.
À l’inverse, des systèmes comme TOMAMC arrivent préassemblés et prêts à être utilisés. Cela signifie moins de temps d’installation, moins de surprises lors de la configuration et une transition plus rapide vers la production active.
Exigences propres à certains secteurs
Certaines industries nécessitent des caractéristiques dépassant les configurations standards :
- Aliments et boissons : utilisation de matériaux hygiéniques ou de composants lavables à haute pression.
- Produits pharmaceutiques : manipulation de haute précision et systèmes de traçabilité.
- Automobile : charges plus lourdes et équipements à haute vitesse.
Ces exigences supplémentaires peuvent faire augmenter les coûts d’acquisition et d’entretien.
Formation des opérateurs
La formation est souvent incluse avec le système de palettisation, mais la main-d’œuvre et les arrêts liés à la formation influencent tout de même le coût global. Si vous formez trois opérateurs pendant un même quart de travail, le coût ne se limitera pas à leurs salaires – il inclura aussi la perte de production pendant que ces employés ne sont pas à leur poste. Même avec des systèmes faciles à utiliser, une formation de base est nécessaire pour naviguer dans l’IHM, effectuer un redémarrage après un arrêt ou faire des ajustements courants.
L’interface MOVNMC de TOMAMC est conçue pour être si intuitive que la plupart des utilisateurs peuvent l’utiliser avec un minimum d’instructions. Dans bien des cas, une formation formelle devient optionnelle plutôt qu’obligatoire, ce qui réduit le temps de mise en route et les coûts associés.
Premier Tech propose plusieurs options de formation pour TOMAMC :
- Modules en ligne à votre rythme pour une intégration rapide.
- Journées de formation sur site en option, adaptées à votre équipe.
- Forfaits de formations personnalisées pour les grands clients avec des équipes de formation internes.
- Outils d’apprentissage ludiques utilisant des plateformes de type jeu vidéo pour améliorer l’engagement et la rétention.
Premier Tech dispose également d’une équipe dédiée à la formation disponible toute l’année, ce qui permet aux clients de renforcer les compétences en interne et de maintenir des équipes confiantes et compétentes à long terme.
Équipement de sécurité
Si votre système de palettisation n’intègre pas de dispositifs de sécurité, il peut être nécessaire d’ajouter des éléments de protection, tels que des clôtures ou des rideaux lumineux. L’ajout de ces éléments dépend de plusieurs facteurs : taille de la charge, vitesse de palettisation, configuration de l’espace de travail et résultats de votre analyse de risques.
En Amérique du Nord, la responsabilité de l’analyse de risques incombe à l’utilisateur final, c’est-à-dire le fabricant. Bien que de nombreuses entreprises respectent les normes officielles en matière de sécurité, il est fréquent d’y ajouter des protocoles internes. Les grandes organisations disposent souvent d’équipes EHS (environnement, hygiène et sécurité) ou d’ingénieurs en sécurité chargés d’implanter des mesures supplémentaires pour réduire les risques et répondre aux exigences des assureurs.
Ces dispositifs de sécurité additionnels peuvent faire augmenter les coûts initiaux du système, il est donc essentiel de les inclure dès les premières étapes de planification et de budgétisation.
Comment estimer le RSI de votre robot de palettisation
Un calcul de RSI solide doit prendre en compte l’impact global du système de palettisation sur vos opérations.
Réduction de la main-d’œuvre
Commencez par estimer le nombre de quarts de travail et le nombre de travailleurs que le système pourrait remplacer ou soutenir. La plupart des outils simples de calcul du RSI s’appuient sur cette formule :
RSI = coût total du système ÷ coût de la main-d’œuvre manuelle remplacée
Bien qu’utile comme point de départ, ce calcul ne montre qu’une partie de la réalité. Il omet des éléments essentiels qui peuvent déterminer la vraie valeur de votre investissement à long terme.
Facteurs qui influencent le RSI réel
Un calcul plus approfondi devrait également tenir compte des éléments suivants :
- L’efficacité des travailleurs comparativement à celle des robots lors de longs quarts de travail ou en présence de plusieurs UGS.
- Les coûts d’exploitation annuels, comme l’énergie, l’entretien et la formation.
- La réduction des pertes de produits grâce à un empilage plus uniforme ou à une diminution des chutes de charge.
- L’amélioration du temps de cycle, qui augmente le taux de production et élimine les goulots d’étranglement.
- La stabilité du temps de fonctionnement, surtout lorsqu’on remplace des tâches physiquement exigeantes qui causent de la fatigue ou des erreurs fréquentes.
Sans ces variables, vous ne pouvez pas visualiser le rendement complet que votre système peut réellement offrir.
Vous souhaitez savoir combien coûte un palettiseur collaboratif et quel sera son impact sur votre rentabilité?
Estimez votre retour sur investissement grâce au calculateur FriendustrialMC de RSI pour palettiseur collaboratif, et découvrez comment vos données de production influencent les coûts, la rentabilité et les économies à long terme.
Choisir la bonne solution pour votre installation
Le bon système de palettisation est celui qui correspond à vos opérations actuelles tout en soutenant votre croissance future – et non celui qui a simplement le prix le plus bas.
- Adaptez le système à votre volume de production et à la diversité de vos produits. Les lignes à haute vitesse avec des produits uniformes bénéficieront davantage de systèmes conventionnels ou robotisés classiques. Pour des lignes à volume plus faible ou comportant des UGS variées, les robots sont souvent plus adaptés.
- Tenez compte du niveau de compétence technique de votre équipe. Certains systèmes nécessitent un soutien continu en programmation, tandis que d’autres utilisent des interfaces simples que votre personnel peut gérer à l’interne.
- Pensez à long terme. Évaluez la capacité du système à s’adapter à l’évolution de vos types de produits, de votre volume de production ou de vos lignes d’emballage. Le coût total de possession dépend souvent de la flexibilité offerte par le système au fil du temps.
Conclusion
Un bon système de palettisation doit rendre vos opérations plus rapides, plus stables et plus faciles à faire évoluer.
Les systèmes conventionnels offrent un taux de production maximal. Les systèmes robotiques vous offrent plus d’adaptabilité. TOMAMC va encore plus loin en combinant le meilleur des deux mondes, avec un accent sur la simplicité et la fiabilité.
TOMAMC est la combinaison d’un taux de production stable et de haute qualité, d’une grande flexibilité, d’une utilisation simplifiée et de composants prêts à l’emploi. Fort de l’expertise technique acquise par Premier Tech depuis plus de 35 ans, TOMAMC intègre la technologie robotique éprouvée de FANUC dans un seul système facile à déployer, conçu pour la simplicité et la performance.
Investissez dans une solution de palettisation qui fonctionne pour vos besoins d’aujourd’hui, tout en soutenant vos objectifs de demain.
Vous vous demandez si la solution de palettisation TOMAMC convient à vos opérations?
Répondez à quelques questions pour trouver la solution la mieux adaptée à vos besoins. Le processus ne prend que quelques minutes et vous fournira des informations précieuses pour déterminer comment TOMAMC peut s’intégrer à vos opérations.
Vous cherchez quelque chose de simple et sans code ?
TOMAMC se consacre à rendre l'automatisation Friendustrial™, et notre équipe a rendu la puissance des cobots accessible d'une toute nouvelle manière. Découvrez-en plus sur nos produits.