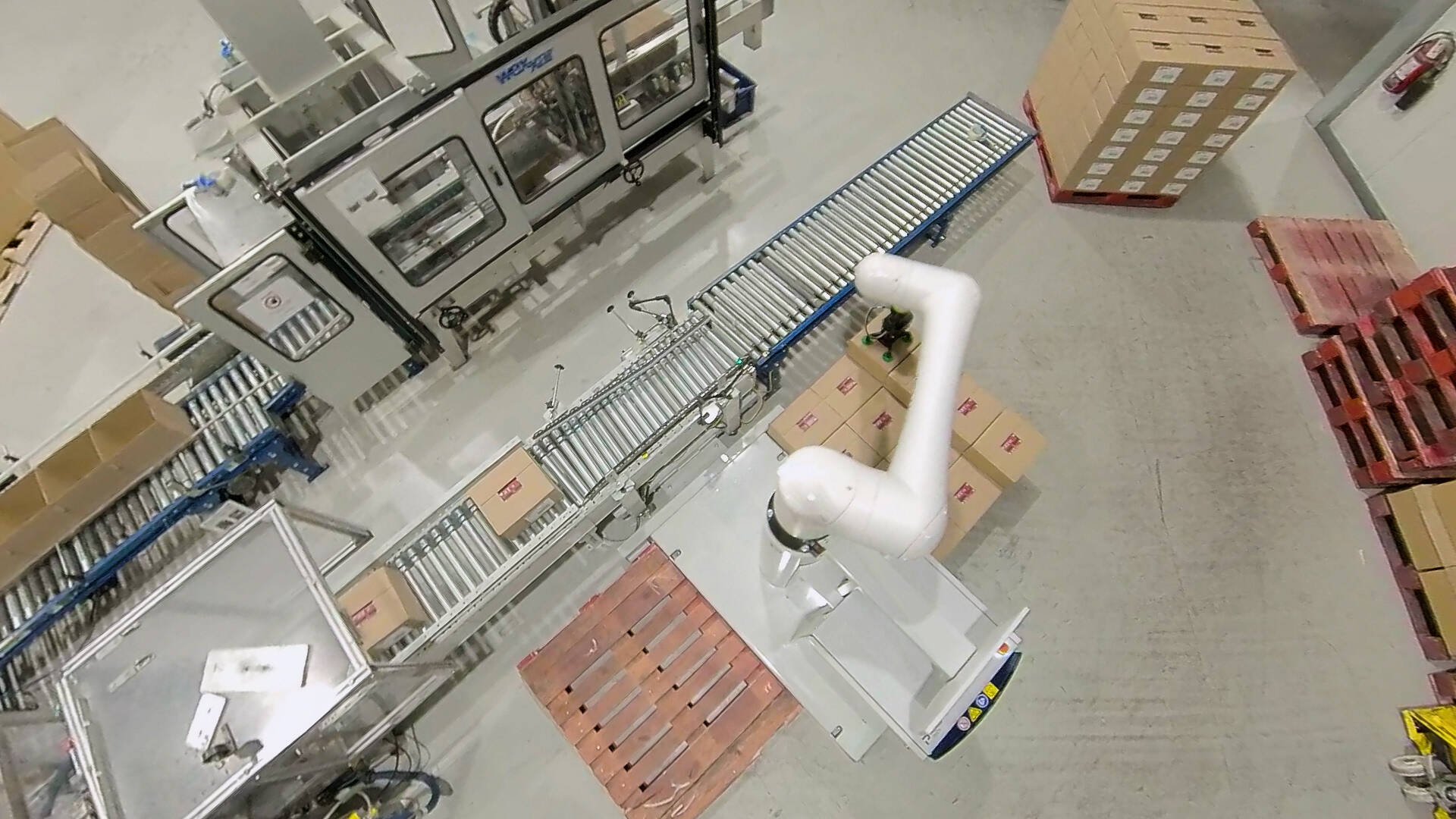
How Much Does a Robotic Palletizer Cost? Factors That Influence Your Investment
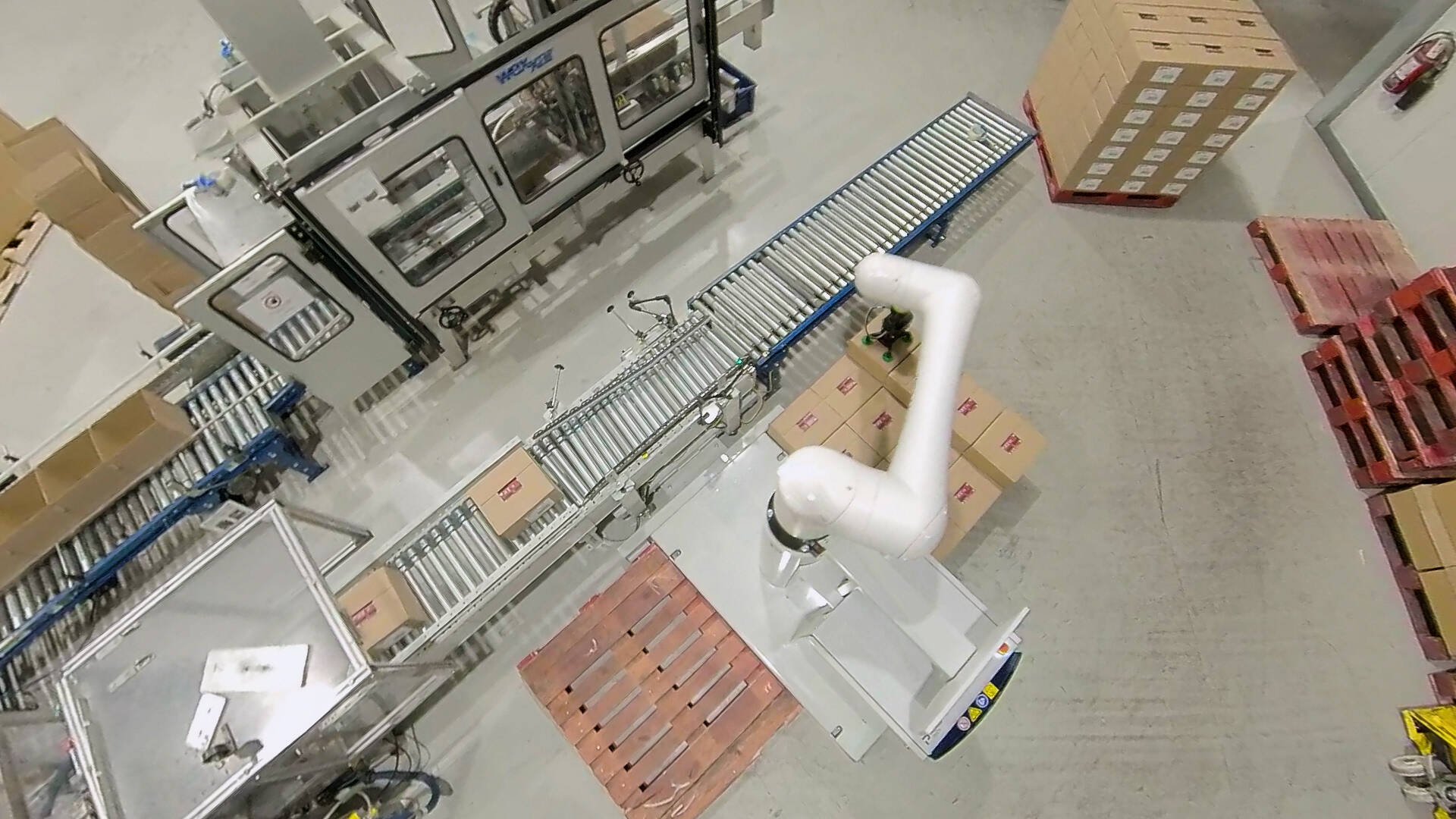
Explore robotic palletizer costs, key pricing factors, and how to estimate ROI for the right palletizing solution for your facility.
If your end-of-line operations are struggling to keep up with rising output, robotic palletizing may already be on your radar.
Robotic palletizers automate repetitive end-of-line tasks, improving speed, consistency, and safety. They’re also flexible enough to scale with production demands.
As automation becomes more common, one key question remains: what will it cost to implement a robotic palletizer?
The answer depends on several factors, including system design, throughput needs, and how well the solution fits into your existing workflow. Understanding these variables is key to making a smart investment.
In this guide, we will break down typical cost ranges, what drives pricing, and how to determine whether a robotic palletizer is the right fit for your operation.
How Much Does a Palletizing System Cost?
Palletizing systems vary widely in price depending on the type of technology used, production speed, level of automation, and integration requirements. Here’s a general look at typical price ranges:
- Manual and semi-automatic systems: From workers' compensation to very variable, depending on how automated the palletizer is.
- Conventional systems: Typically priced between $275,000 and $1,000,000, depending on speed (BPM or CPM), layout, and product type.
- Robotic systems (traditional and cobot): These start around $100,000 for simpler cobot units and can reach up to $900,000 for higher-speed robotic arms handling complex patterns or heavier payloads.
- Hybrid systems: Highly variable depending on the needs, but can reach up to $1M+.
Pricing can shift significantly based on throughput, level of automation, and how much customization your operation requires. These figures provide a general starting point, but a more accurate estimate depends on the specific requirements of your system.
Why Cobot Palletizers Are a Smart Entry Point
If you're looking for a solution that doesn't require a full layout redesign, cobot palletizers offer a more accessible path to automation. Compact, safe to work around, and simple to program, they are often ideal for facilities taking their first step into robotic palletizing.
The TOMA™ Palletizer uses cobot technology in a standardized platform that’s fast to deploy and easy to operate. Built around MOVN™, the most advanced intuitive interface on the market, it’s designed to make palletizing more accessible without compromising safety, stability, or performance.
Want to understand how much a cobot palletizer can cost and impact your bottom line?
Estimate your ROI with the FriendustrialTM Cobot Palletizer ROI Calculator and see how your production inputs impact cost, payback, and long-term savings.
What Influences the Cost of a Palletizing System?
From how fast your line moves to how your facility is laid out, every detail plays a part in the cost.
1. System Type
The type of palletizing system you choose plays a major role in both cost and long-term value.
- Manual and semi-automatic systems: Lowest upfront cost, but rely heavily on manual labor and offer limited scalability.
- Conventional systems: Built for speed and volume. These large, mechanical systems come at a higher price point due to their complexity.
- Robotic systems: Includes traditional industrial arms or collaborative robots. Pricing depends on cycle speed, payload, programming needs, and flexibility.
- Hybrid systems: Custom-engineered solutions that blend technologies. Typically, the most complex and difficult to price without a detailed system review.
Some systems are easier to install, require less training, and include intuitive controls for everyday operation. These differences influence labor needs, integration costs, and maintenance, and they directly impact how soon you’ll see a return on your investment.
2. Throughput Speed
Higher speeds typically require stronger frames, faster actuators, and more advanced controls. This adds to the overall price.
- Conventional palletizers are built for high-speed production and can handle large volumes with minimal variation. They are typically used in facilities that run high-throughput lines with repeatable patterns.
- Traditional robotic systems also support moderate to high speeds, offering flexibility in product types and pallet patterns while maintaining steady output. These are well-suited for operations balancing volume with some variation.
- Cobots are ideal for low to medium throughput environments. They’re not as fast as industrial systems, but they’re easier to use, safer, and more adaptable, especially when batch sizes or production runs vary.
Operations with continuous, high-volume output typically face higher upfront costs. Achieving high-speed performance often requires additional investment in tooling, conveyors, and integration to keep the system aligned.
3. Level of Automation
The level of automation built into your palletizing system affects both cost and complexity.
- Semi-automated systems: Operators are still involved in tasks like manual product loading or pallet handling. These systems cost less but rely more on labor.
- Fully automated systems: Handle product detection, stacking, and pallet exchange without manual input. These require advanced controls, safety protocols, and integration with upstream and downstream equipment.
Higher levels of automation often require more programming and setup time. While operator involvement decreases, some training is still necessary to handle the HMI, restart the system, and make minor adjustments. The upfront investment is higher, but long-term labor costs may be lower.
4. End-of-Arm Tooling (Grippers)
Grippers are one of the most important components of any palletizing system. The right tooling depends on the type, shape, and weight of the products you are handling.
- Bags: Often require mechanical or clamp-style grippers to maintain control over shifting weight.
- Cases and boxes: Typically use vacuum or suction grippers for flat, rigid surfaces.
- Fragile or irregular items: May need custom or hybrid tooling to prevent product damage.
The more specialized the product, the more complex and costly the gripper. Tooling affects both the initial system price and long-term costs, especially if frequent product changeovers require adjustments or replacements.
5. Sensors, Vision, and Conveyors
Sensors and conveyors are integral components that significantly influence the efficiency and cost of a palletizing system.
- Sensors & Vision: Utilized for tasks such as box detection, orientation, and quality control, sensors and vision systems ensure accurate product placement and system reliability. Advanced setups can detect various package types, including glossy, dark, or stretch-wrapped items.
- Conveyors: Responsible for moving products into the correct position for palletizing. Conveyor design, speed, and length all influence cost. Additional features like diverting arms, powered rollers, or slide gates can raise conveyor system pricing by $10,000 to $50,000 or more, depending on the layout.
Component quality and complexity have a direct impact on integration costs. High-quality sensors and well-designed conveyors can improve efficiency but raise initial expenses. Lower-end components may cost less upfront but often lead to more maintenance and reduced reliability over time.
6. Integration Requirements
Integration adds time, cost, and complexity, especially when a palletizer needs to connect with other systems on your line. From conveyors and case packers to stretch wrappers, labelers, and warehouse management software, the more equipment you need to sync, the more planning and engineering is involved.
- System connectivity: Palletizers often interface with upstream or downstream machines and may also need to connect with ERP systems or plant-level controls. This requires compatibility with your existing digital infrastructure and may involve additional software or middleware.
- Retrofitting into existing lines: Some operations can reduce integration costs by placing the palletizer in an existing manual station or using current conveyors. Compact or modular units are generally easier to install with minimal changes to your layout.
- Custom engineering: The more customized the integration, the more likely you’ll need PLC programming, I/O mapping, and synchronization with legacy systems. This drives up both engineering time and commissioning cost.
This is where standardized solutions like TOMA™ can simplify the process. TOMA™ uses cobot technology in a pre-engineered platform that’s designed to reduce integration complexity. With built-in tools, a streamlined HMI, and a compact footprint, it’s built for fast deployment and a shorter path to production.
Learn more about the TOMA™ cobot palletizer and how it can speed up your palletizing process.
7. Maintenance and Upkeep
Ongoing maintenance is part of any palletizing system’s total cost of ownership. This includes inspections, wear part replacements, and occasional service support.
- What’s included: Scheduled checks, basic wear items (like suction cups or conveyor bands), battery replacements, and software updates.
- Typical annual cost: For most systems, maintenance ranges between 3–10% of the purchase price. For example, a conventional palletizer priced at $750,000 may see $22,500–$75,000 annually.
However, standardized solutions like TOMA™ are designed for minimal upkeep. With no robot maintenance needed for up to 8 years and limited wear items, typical annual costs often stay under $2,000.
Ask your provider for an estimated maintenance cost based on your system type and usage.
8. Operating & Overhead Costs
The total cost of a palletizing system goes beyond the purchase price. Operating expenses like electricity, depreciation, and training all factor into your long-term ROI.
- Power consumption: Larger systems consume more energy and may cost significantly more depending on runtime and load.
- Depreciation: Most palletizers can be depreciated up to a 10-year period, allowing you to recover part of the cost through tax deductions while still accounting for the capital investment.
These ongoing costs accumulate over time and should be factored into any accurate ROI or budgeting model.
Additional Cost Variables to Keep in Mind
Beyond the system and integration costs, there are several overlooked expenses that can impact your total investment. These costs may not show up in the quote but still affect your bottom line over time.
Installation Costs
Installation costs vary depending on the complexity of the system, your facility’s location, whether you have an in-house automation team, and how much integration is required. Systems that need custom programming, multiple connection points, or adaptation to tight spaces often take longer to install and commission.
Some palletizing solutions arrive in multiple parts and require additional time on-site for mechanical and software assembly. This not only extends setup time but can also delay production startup if internal resources are limited.
By contrast, systems like TOMA™ arrive fully assembled and ready to use. That means less time spent on installation, fewer surprises during setup, and a faster transition to live production.
Industry-Specific Requirements
Some industries require features that go beyond standard configurations:
- Food and beverage: Systems may need hygienic materials or washdown-rated components.
- Pharmaceuticals: High-precision handling and traceability features are often necessary.
- Automotive: Applications often call for heavier payloads and higher-speed equipment.
These added requirements can raise both acquisition and maintenance costs.
Operator Training
Training is often included with a palletizing system, but labor and downtime during onboarding still affect your overall cost. If you're training three operators during a single shift, the expense isn’t just wages, it also includes lost production while those employees are off the line. Even with user-friendly systems, basic instruction is needed to navigate the HMI, reset after stops, and make routine adjustments.
TOMA’s interface, MOVN™, is designed to be so straightforward that most users can operate it with minimal instruction. In many cases, formal training becomes optional rather than required, which shortens ramp-up time and reduces cost.
Premier Tech offers several training options for TOMA:
- Online self-paced module for quick onboarding
- Optional on-site training days tailored to your team
- Custom training packages for larger clients with internal training teams
- Gamified learning tools using video game-style platforms to improve engagement and retention
Premier Tech also has a dedicated training team available year-round, making it easier for clients to scale knowledge internally and keep their teams confident and capable over time.
Safety Equipment
If your palletizing system doesn’t include built-in safety features, you may need to add physical barriers such as guarding, fencing, or light curtains. Whether or not these upgrades are necessary depends on factors like payload size, palletizing speed, workspace layout, and the results of your risk assessment.
In North America, the responsibility for conducting a risk assessment falls on the end user—the manufacturer. While many companies follow official safety standards, it’s also common to see internal safety protocols layered on top. Larger organizations often have dedicated EHS teams or safety engineers who implement additional measures to reduce risk exposure and meet corporate insurance requirements.
These added safety components can increase the upfront cost of your system, so it’s important to account for them early in the planning and budgeting process.
How to Estimate ROI for Your Palletizing Robot
A solid ROI calculation should account for the full impact of a palletizing system across your operations.
Labor Reduction
Start by estimating how many shifts and how many workers the system could replace or support. Most simple ROI tools focus on this equation:
ROI = Total system cost ÷ Annual manual labor cost being replaced
While helpful as a starting point, this only shows part of the picture. It leaves out the details that make or break the long-term value of your investment.
Factors That Affect Real ROI
A deeper calculation should also consider:
- Worker efficiency vs. robot efficiency over long shifts or multiple SKUs.
- Annual operating costs like energy, maintenance, and training.
- Reduced product waste from more consistent stacking or fewer dropped loads.
- Improved cycle time, which increases throughput and clears bottlenecks.
- Uptime stability, especially when replacing physically demanding roles that lead to operator fatigue or frequent errors.
Without these variables, you're not seeing the full return your system could deliver.
Want to understand how much a cobot palletizer can cost and impact your bottom line?
Estimate your ROI with the FriendustrialTM Cobot Palletizer ROI Calculator and see how your production inputs impact cost, payback, and long-term savings.
Choosing the Right Fit for Your Facility
The right palletizing system is one that fits your current operation and supports future growth, not the one with the lowest price.
- Match the system to your production volume and product mix. High-speed lines with repeatable products may benefit from conventional or traditional robotic systems. Mixed SKUs or lower-volume lines might be better served by robots.
- Factor in your team’s technical comfort level. Some systems require ongoing programming support, while others use simple interfaces that your in-house team can manage.
- Think long-term. Consider how easily the system can adapt if your product types, throughput, or packaging lines evolve. Total cost of ownership often comes down to how much flexibility the system gives you over time.
Conclusion
The right palletizing system should make your operations faster, more consistent, and easier to scale.
Conventional systems offer maximum throughput. Robotic systems give you more adaptability. TOMA™ takes it further by combining the best of both worlds with a focus on simplicity and reliability.
TOMA™ is where high-quality, stable production rates meet flexibility, ease, and plug-and-play functionality. Backed by over 35 years of Premier Tech’s technical expertise, TOMA™ combines FANUC’s proven robotic technology into a single, easy-to-deploy system designed for simplicity and performance.
Buy a palletizing solution that works for your operation today and supports your goals for tomorrow.
Wondering if TOMA™ palletizing solution is a good fit for your operation?
Answer a few questions to help find the best fit for your needs. The process should only take a few minutes and provide valuable information to determine how TOMA™ fits in your operation.
Looking for something simple and code-free?
TOMA™ is all about making automation Friendustrial™, and our team has made the power of cobots accessible in an all-new way. Learn more about our products.