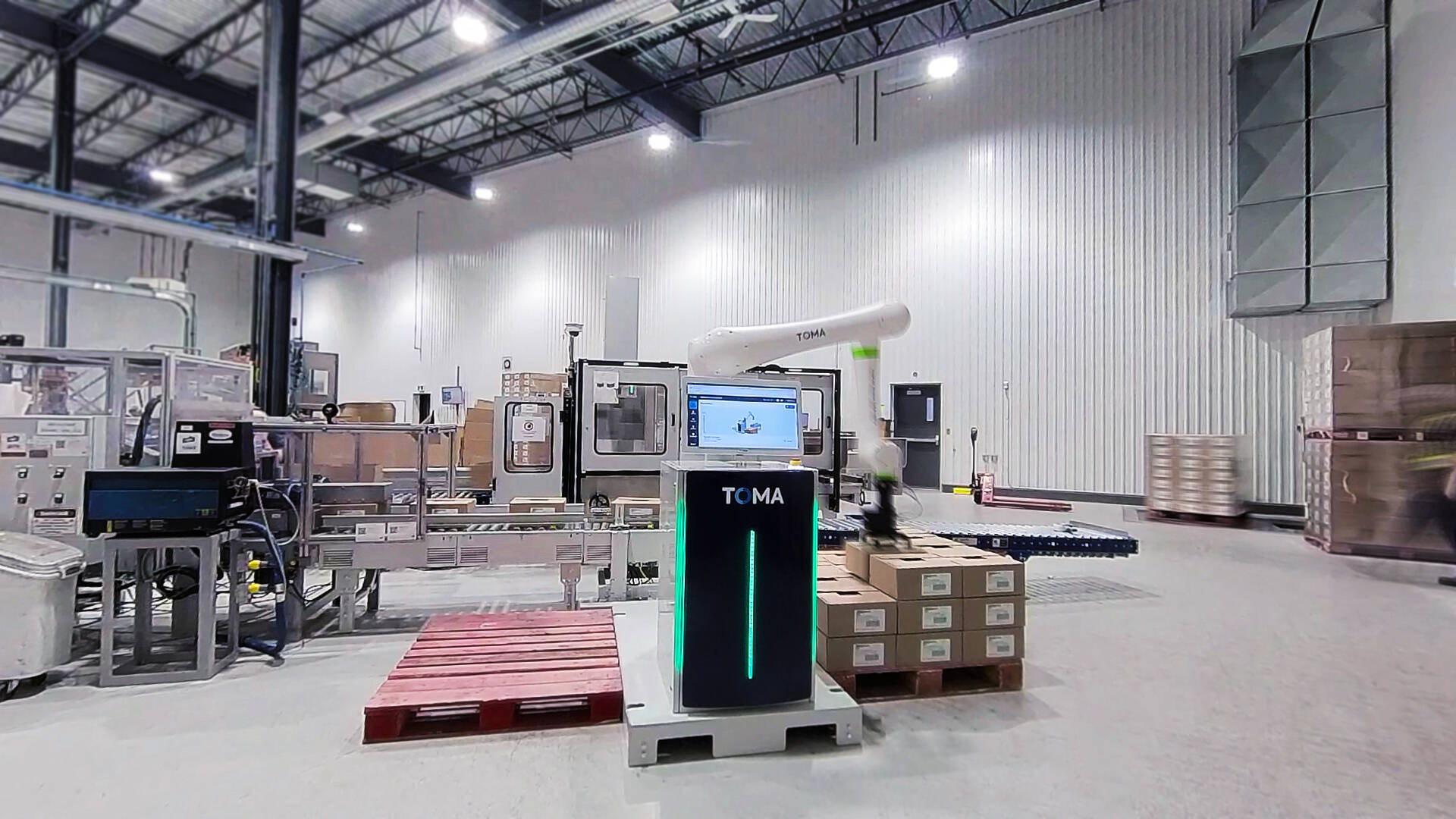
Types de palettiseurs : Choisir la meilleure option pour vos opérations
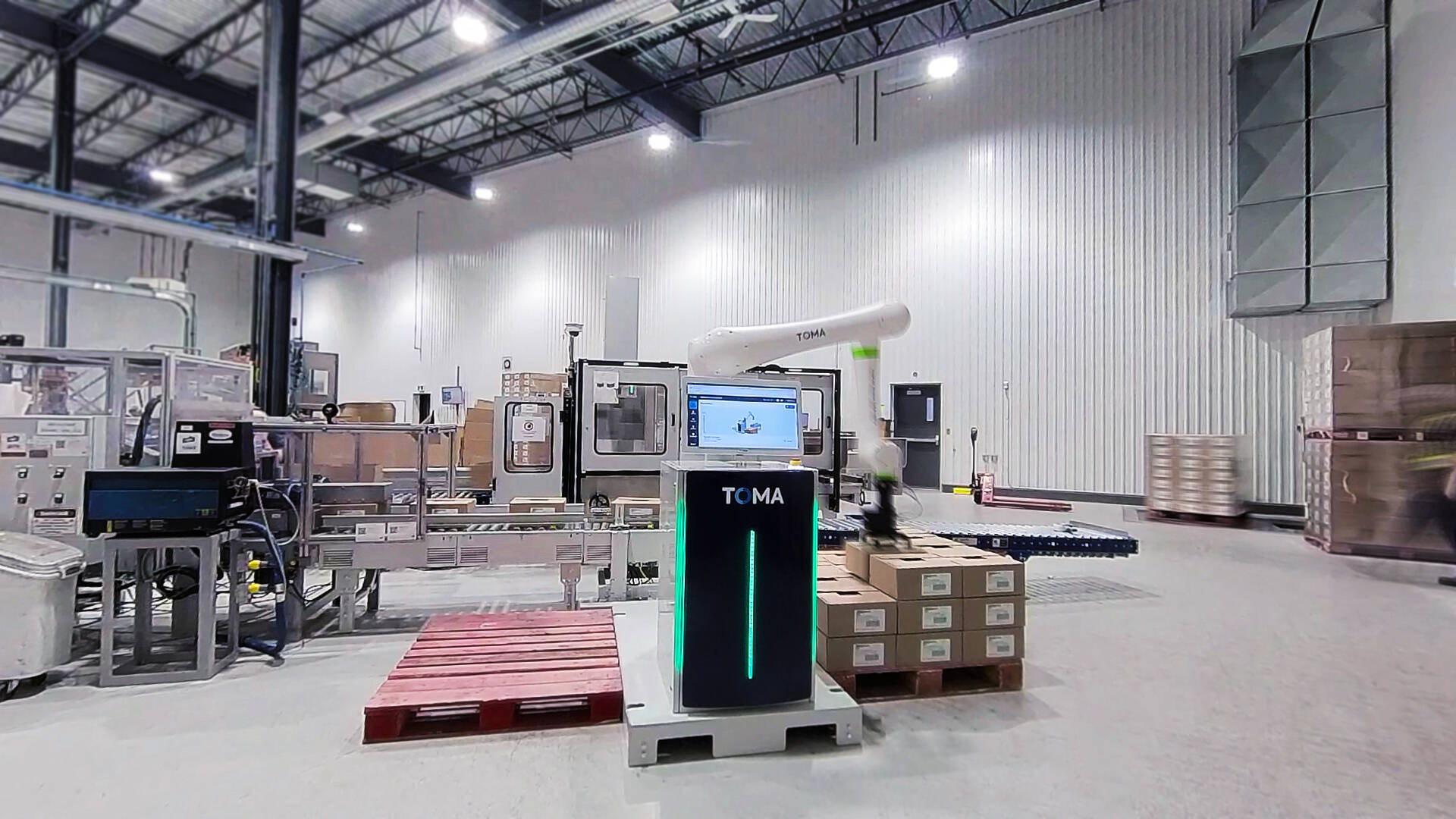
Comparez les types de palettiseurs et choisissez le système adapté à vos opérations. Explorez les options manuelles, conventionnelles, robotisées et collaboratives selon la vitesse, l’espace disponible et l’utilisation.
Choisir le bon palettiseur commence par comprendre vos besoins de production. Que vous fassiez face à des pénuries de main-d'œuvre, à des espaces restreints ou à une grande variété de références (UGS), le bon système de palettisation peut avoir un impact décisif sur l’efficacité de votre ligne.
Ce guide présente les principaux types de palettiseurs et vous aide à choisir celui qui correspond à vos contraintes d’espace, de vitesse et de main-d'œuvre.
Les principaux types de palettiseurs (et où ils s’adaptent le mieux)
La meilleure solution de palettisation dépend du volume de votre production, de la configuration de votre installation et des ressources de main-d'œuvre disponibles.
Palettiseurs manuels et semi-automatiques
Les palettiseurs manuels et semi-automatiques conviennent le mieux aux opérations à faible volume et aux budgets limités. Ces systèmes utilisent souvent des outils comme des palonniers à ventouses ou des tables élévatrices pour réduire la fatigue physique des travailleurs, mais reposent encore largement sur la main-d'œuvre manuelle.
Idéal pour : Faible volume, opérations avec un budget limité.
Avantages :
- Faible coût initial
- Formation minimale requise pour les opérateurs
Inconvénients:
- Grande dépendance à la main-d'œuvre
- Débit de production limité
- Risque accru de blessures liées aux mouvements répétitifs
Palettiseurs conventionnels
Les palettiseurs conventionnels sont des machines entièrement automatisées qui empilent les produits sur des palettes à l’aide de systèmes mécaniques de formation de couches. Ils reçoivent généralement les produits via un convoyeur, les organisent en couches, puis déposent chaque couche sur une palette.
Ces systèmes sont idéals pour manipuler de grands volumes de produits uniformes avec un minimum de changements.
- Idéal pour : La production à volume élevé avec une seule référence (UGS)
Sous-types :
Palettiseurs à niveau élevé : fonctionnement plus rapide et encombrement réduit Palettiseurs à niveau bas : plus facile à entretenir, mais généralement plus lent
Avantages :
- Grande fiabilité et temps de fonctionnement élevés
- Cycles rapides
- Palettes stables et uniformes
Inconvénients :
- Flexibilité limitée en cas de changement de UGS
- Temps de changement plus longs
- Nécessite plus d’espace au sol
Palettiseurs robotisés
Les palettiseurs robotisés sont des systèmes automatisés qui utilisent un bras robotisé articulé pour saisir et déposer les produits sur les palettes. Ils offrent un haut niveau de flexibilité et sont particulièrement utiles dans les environnements manipulant une grande variété d’UGS, de tailles de produits ou de types d’emballages.
Selon l’application, ces systèmes peuvent manipuler les produits un par un, par rangée ou par couche, selon l’outil utilisé en bout de bras (EOAT).
Ils conviennent parfaitement aux environnements de production à volume moyen ou élevé, où l’on recherche à la fois une qualité de palettisation constante et une adaptabilité aux variations de productions.
Technologies robotiques :
Il existe deux principaux types de technologies de palettisation robotisée:
- Robots traditionnels : Conçus pour les applications à haute vitesse et charge élevée. Souvent utilisés dans des systèmes sur mesure avec une infrastructure de sécurité dédiée.
- Robots collaboratifs (Cobots) : Conçus pour un usage collaboratif, avec des fonctions de sécurité intégrées permettant leur utilisation dans des espaces partagés, lorsqu’ils sont correctement configurés.
Modèles de livraison des systèmes : Les palettiseurs robotisés peuvent être livrés sous différentes formes, selon les objectifs de l’installation.
- Systèmes sur mesure : Adaptés à des lignes de production spécifiques avec des exigences complexes. Occasionnent souvent des délais d’intégration plus longs et un coût initial plus élevé.
- Solutions standardisées : Systèmes préconçus, plus rapides à déployer et plus simples à utiliser. Ils incluent généralement une interface IHM dédiée, des convoyeurs intégrés et une configuration « plug and play ».
À propos des palettiseurs collaboratifs (Cobots)
Les palettiseurs collaboratifs (Cobots) sont un type de système robotisé conçus spécifiquement pour les applications de palettisation collaborative. Leur conception flexible et compacte les rend parfaits pour les environnements à faible ou moyen volume, les changements fréquents d’UGS et les installations disposant de peu d’espace au sol. Les palettiseurs collaboratifs (Cobots) sont faciles à déplacer, rapides à reprogrammer et permettent un redéploiement rapide sur différentes lignes. Bien qu’ils soient conçus pour une utilisation sécuritaire en milieu collaboratif, la norme ISO 10218:2025 précise que la sécurité dépend de l’ensemble du système, et non seulement du bras robotisé. L’outillage, la charge utile, la vitesse, la configuration des lieux et l’application en général doivent tous être pris en compte.
Idéal pour : Les installations cherchant une automatisation modulaire avec un minimum de perturbation.
Avantages :
- Prend en charge une grande variété de produits et de formats d’emballage
- Conception modulaire facilitant une mise en œuvre progressive et une expansion future
- Les palettiseurs collaboratifs (Cobots) offrent une grande flexibilité avec un redéploiement simplifié et une configuration rapide.
Inconvénients :
- Capacité de charge plus faible et vitesses plus lentes
- Une formation spécialisée peut être requise pour les configurations avancées
Le palettiseur TOMA™ est le système de palettisation standardisé de Premier Tech, basé sur la technologie des robots collaboratifs (Cobots). Il combine la flexibilité des cobots avec la fiabilité et la simplicité d’utilisation attendues d’une plateforme de palettisation complète.
Avec une configuration rapide des recettes, des convoyeurs intégrés et une interface IHM intuitive, le palettiseur TOMAMC est conçu pour les fabricants souhaitant automatiser sans complexité ni ingénierie sur mesure.
Découvrez-en plus sur le palettiseur TOMA🅪, basé sur la technologie des robots collaboratifs (Cobots) et voyez comment il peut accélérer votre processus de palettisation.
Palettiseurs hybrides
Les palettiseurs hybrides combinent les éléments des systèmes robotisés et conventionnels afin de répondre à des besoins de productions spécifiques. Ils sont généralement utilisés lorsqu’une solution standard ne permet pas d’atteindre la vitesse, la flexibilité ou la capacité de manipulation des produits nécessaires.
Idéal pour : Scénarios personnalisés où ni la solution robotisée ni la solution conventionnelle seule ne suffit.
Avantages :
- Grande flexibilité avec une débit plus élevé
- Capables de gérer des schémas de palettisation complexes ou des produits de tailles variées
- Utiles pour des configurations particulières ou des besoins à grande vitesse
Inconvénients :
- Complexité plus élevée en conception et en intégration
- Nécessite souvent une ingénierie sur mesure et un soutien personnalisé
Comment choisir un palettiseur qui répond réellement à vos besoins
Maintenant que vous avez exploré les différents types de palettiseurs, il est temps de vous concentrer sur celui qui convient le mieux à votre opération.
Le choix du bon système commence par une compréhension claire du fonctionnement actuel de votre ligne et des défis que l’automatisation doit résoudre.
Utilisez ces questions pour orienter votre décision :
1. Quels types de produits allez-vous palettiser ?
Sacs lourds, boîtes légères ou contenants irréguliers? La forme, la taille et la rigidité de vos produits détermineront le type de préhenseur nécessaire ainsi que la stabilité des palettes. Ces informations forment la base pour tout le reste.
2. Combien de références UGS gérez-vous et à quelle fréquence changent-elles ?
Si vous changez de produits ou de schémas de palettisation plusieurs fois par quart de travail, vous aurez besoin d’un système capable de s’adapter rapidement sans devoir faire appel à un programmeur. Dans ce cas, la flexibilité et la facilité de changement sont plus importants que la vitesse brute.
3. Quel débit visez-vous ?
Votre objectif en caisses par heure vous aidera à filtrer rapidement les options. Les lignes à haute vitesse peuvent justifier des systèmes plus spécialisés. Des volumes plus faibles ou saisonniers peuvent mieux convenir à une solution modulaire ou redéployable.
4. Disposez-vous de ressources internes pour entretenir le système ?
Les systèmes très personnalisés exigent souvent des connaissances spécialisées, des contrats de service externes ou des délais de réponse plus longs en cas de problèmes. Si votre équipe ne possède pas d’expertise en automatisation, ou si les arrêts prolongés sont inacceptables, pensez à la maintenance quotidienne et au soutien requis. Les plateformes standardisées sont généralement plus faciles à entretenir en interne et plus rapides à remettre en marche.
5. Votre espace au sol est-il limité ?
Si votre fin de ligne est déjà encombrée, optez pour des systèmes compacts avec sécurité intégrée ou intégration verticale. Les systèmes conventionnels de grande taille peuvent ne pas convenir sans une reconfiguration majeure de l’espace.
6.Recherchez-vous un système sur mesure ou une solution prête à l’emploi ?
Les solutions personnalisées peuvent tout faire, mais elles demandent plus de temps et d’investissement. Les systèmes standardisés sont plus rapides à installer et plus simples à prendre en main, surtout pour des équipes sans expérience en automatisation.
7. Quel est le principal moteur de votre investissement : le coût, la main-d'œuvre, la qualité ou bien tout à la fois ?
Clarifier ce qui motive votre décision permet de mieux cibler vos options. Si le problème est lié à la main d'œuvre, la facilité d’utilisation et la rapidité de mise en service auront plus d’importance que la vitesse de cycle. Si vous cherchez à augmenter le débit, la vitesse et la disponibilité doivent être prioritaires.
Faites notre évaluation via le configurateur afin de savoir si un palettiseur standard come TOMA🅪 peut répondre à la diversité de vos produits, à votre espace disponible et à vos objectifs de production, le tout sans la complexité d’un système sur mesure.
Une meilleure solution pour la production moderne
Ce ne sont pas toutes les usines qui ont besoin d’un système entièrement personnalisé. Et ce ne sont pas tous les palettiseurs standards qui sont conçus pour s’adapter. C’est là que TOMA🅪 entre en jeu. Le palettiseur TOMA🅪 est un système robotisé standardisé conçu pour simplifier l’automatisation de fin de ligne. Il répond aux besoins réels de la production : mise en marche rapide, utilisation intuitive et flexibilité pour évoluer avec vos besoins.
- L’interface MOVN🅪 IHM offre l’une des expériences utilisateurs les plus simples de l’industrie. En effet, aucun codage n’est requis pour créer ou modifier des recettes de palettisation.
- Le palettiseur collaboratif (Cobot) FANUC CRX-30iA manipule des charges jusqu’à 25 kg (55 lbs) et offre une performance collaborative efficace avec jusqu’à huit prises par minute.
- Les deux convoyeurs d’entrée intégrés permettent une palettisation simultanée à partir de deux lignes distinctes de 1,2 mètre (4 pieds).
- Le système de surveillance Necton🅪 fournit des données en temps réel pour aider vos équipes à éviter les arrêts et à améliorer l’efficacité.
TOMA🅪 est conçu pour offrir des solutions de palettisation robotisée intuitives. Il aide les fabricants à réduire la complexité, à améliorer la constance et à s’adapter aux changements sans avoir besoin d’un système sur mesure.
Découvrez-en plus sur le palettiseur TOMA🅪 qui utilisent la technologie des robots collaboratifs (Cobots) et voyez comment il peut accélérer votre processus de palettisation.
Trouvez la meilleure solution de palettisation automatisée pour vos opérations
Le bon système de palettisation doit s’aligner avec le fonctionnement réel de votre production. Il doit pouvoir manipuler vos types de produits spécifiques, s’intégrer à votre espace et soutenir vos objectifs à court et long terme.
Que vous cherchiez à réduire le travail manuel, augmenter le débit ou simplifier les tâches répétitives, la solution choisie doit fonctionner avec votre disposition actuelle et évoluer avec vos besoins futurs.
Chez Premier Tech, nous proposons des solutions de palettisation qui s’adaptent vraiment à votre réalité. Que vous cherchiez à monter en capacité, à intégrer de nouvelles lignes de produits ou à améliorer l’ergonomie au travail, nous développons des solutions qui respectent vos objectifs et qui s’intègrent à vos processus.
FAQ
Les principaux types de palettiseurs sont : manuel et semi-automatique, conventionnel, robotisé (y compris les robots traditionnels, collaboratifs ou standardisés) et les systèmes hybrides. Chaque type répond à des besoins différents selon le volume, la variété des produits et la configuration de l’usine.
Les palettiseurs robotisés offrent une plus grande flexibilité et sont idéaux pour gérer plusieurs UGS ou des types de produits variés. Les palettiseurs conventionnels sont plus rapides pour les opérations à haut volume avec un seul UGS et sont mécaniquement plus simples mais moins adaptables.
Commencez par évaluer votre débit, types de produits, la variabilité des UGS, l’espace disponible et votre capacité de maintenance. Le meilleur palettiseur est celui qui répond à vos besoins actuels tout en soutenant vos objectifs à long terme. Faites notre évaluation via le configurateur.
L’entretien varie selon le type de système. Les systèmes conventionnels nécessitent un entretien mécanique régulier. Les systèmes robotisés ont tendance à demander un entretien moins fréquent, mais peuvent nécessiter des connaissances spécialisées ou une formation pour certaines tâches.
Les palettiseurs sont généralement installés à la fin d’une ligne d’emballage et peuvent être intégrés à des convoyeurs, des stations de banderolage et des systèmes d’entreposage. Les systèmes modulaires ou les solutions robotisées standards comme TOMA🅪 facilitent et accélèrent l’intégration.
La sécurité doit être évaluée sur l’ensemble de la cellule de palettisation, pas seulement sur l’équipement lui-même. Cela inclut l’outil en bout de bras (EOAT), la charge utile, la vitesse de fonctionnement, la disposition de la zone de travail et la manière dont le système est utilisé en pratique. Les normes actuelles insistent sur la nécessité d’une évaluation complète des risques et de la mise en œuvre de protections appropriées pour assurer un fonctionnement sécuritaire dans tout environnement. Pour en savoir plus, consultez notre article sur la sécurité en palettisation ici.
Oui, mais ce n’est pas le cas de tous les types. Les systèmes robotisés sont les mieux adaptés à la palettisation multi-UGS, grâce à leur flexibilité et à leurs outils programmables. Les systèmes conventionnels sont généralement conçus pour des charges homogènes avec un seul type de produit.
Vous cherchez le palettiseur adapté à vos besoins ?
Échangez avec un expert Premier Tech et trouvez la solution adaptée à vos besoins.