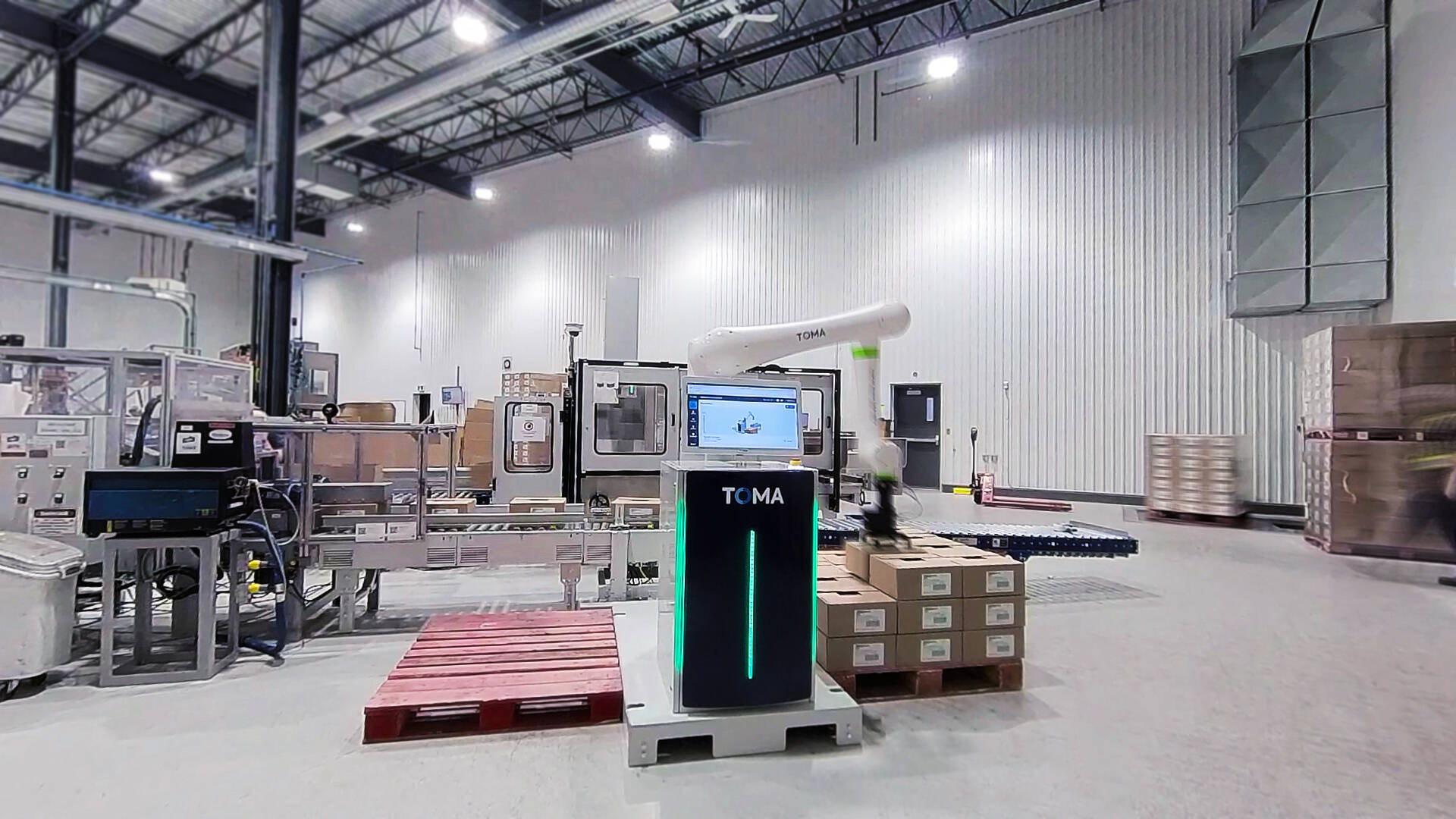
Palletizer types: Choosing the right one for your operations
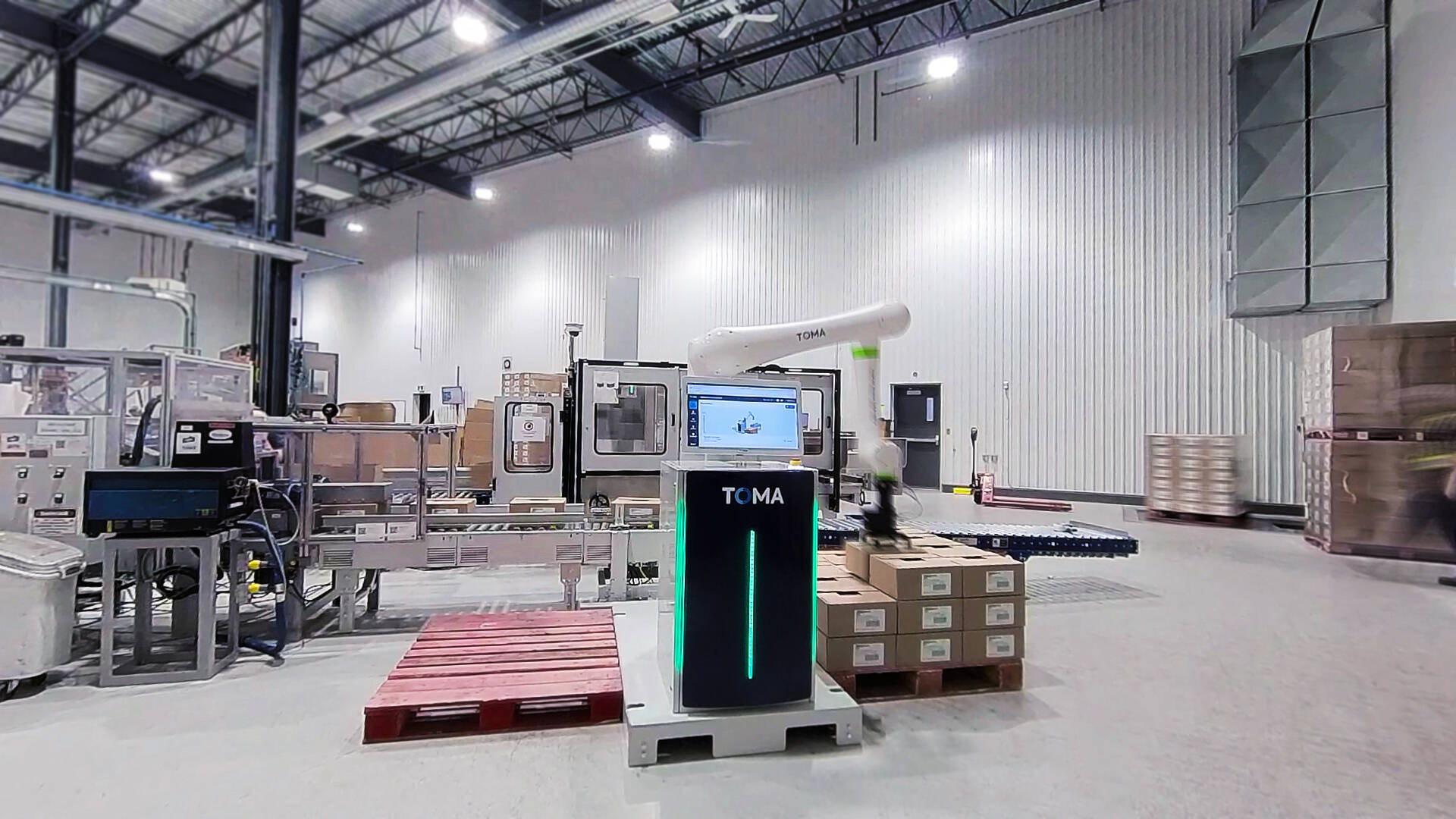
Compare palletizer types and choose the right system for your operation. Explore manual, conventional, robotic, and cobot options by speed, space, and use.
Choosing the right palletizer starts with understanding your production needs. Whether you are dealing with labor shortages, tight layouts, or a mix of SKUs, the right palletizing system can make or break your line’s efficiency.
This guide breaks down the main palletizer types and helps you choose the one that fits your space, speed, and staffing reality.
The main types of palletizers (and where they fit best)
The best palletizer solution depends on your operation's volume, layout, and labor resources.
Manual & semi-automatic palletizers
Manual and semi-automatic palletizers are best suited for low-volume operations with limited budgets. These systems often use tools like vacuum lifters or pallet lift tables to reduce physical strain on workers, but still rely heavily on manual labor.
Good for: Low volume, operations with a tight budget.
Pros:
- Low upfront cost
- Minimal operator training required
Cons:
- Labor-intensive
- Limited throughput
- Higher risk of injury due to repetitive motion
Conventional palletizers
Conventional palletizers are fully automated machines that stack products into pallet loads using mechanical layer-forming systems. They typically receive products from a conveyor, organize them into layers, and place each layer onto a pallet.
These systems are widely used in high-volume production environments where products are uniform and SKU changes are infrequent.
Good for: High-volume, single-SKU production.
Sub-types:
- High-Level Palletizers: Faster operation with a more compact footprint.
- Low-Level Palletizers: Easier to maintain but typically slower.
Pros:
- High reliability and uptime
- Fast cycle times
- Produces stable, uniform pallet loads
Cons:
- Limited flexibility for SKU changes
- Longer changeover times
- Requires more floor space
Robotic palletizers
Robotic palletizers are automated systems that use an articulated robot arm to pick and place products onto pallets. They offer a high degree of flexibility and are especially useful for operations handling a variety of SKUs, product sizes, or packaging types.
These systems can be configured to handle products individually, by row, or by layer depending on the end-of-arm tooling.
They are well-suited for medium-to-high volume environments where consistent pallet quality is needed alongside adaptability to changing production demands.
Robotic Technologies:
There are two main types of robotic palletizing technologies:
- Traditional Robots: Designed for high-speed, high-payload applications. Often used in custom-engineered systems with dedicated safety infrastructure.
- Collaborative Robots (Cobots): Designed for collaborative use, with built-in safety features that support deployment in shared workspaces when properly configured.
System Delivery Models:
Robotic palletizers can be delivered in different formats depending on the facility’s goals.
- Custom-Engineered Systems: Tailored for specific production lines with complex requirements. Often involve longer integration times and higher upfront costs.
- Standardized Solutions: Pre-designed systems that are quicker to deploy and easier to operate. These often come with dedicated HMIs, integrated conveyors, and plug-and-play setup.
More on cobot palletizers
Cobots are a type of robotic system built specifically for use in collaborative palletizing applications. They are designed to be flexible and compact, making them ideal for low-to-medium throughput operations, frequent SKU changes, and facilities with limited floor space.
Cobots are easy to move, quick to reprogram, and typically allow for faster redeployment across different lines. While they are designed for safe use in collaborative settings, ISO 10218:2025 makes clear that safe operation depends on the entire system, not just the robot arm. Tooling, payload, speed, layout, and overall application must all be evaluated. A full risk assessment is always required.
Good for: Facilities needing modular automation with minimal disruption
Pros:
- Handles a wide range of product types and packaging formats
- Modular design supports phased implementation and future expansion
- Cobots add flexibility with easier redeployment and fast setup
Cons:
- Lower payload capacity and slower speeds
- Specialized training may be required for advanced configurations
The TOMA™ Palletizer is Premier Tech’s standardized palletizing system built on collaborative robot technology. It delivers the flexibility of cobots with the reliability and ease-of-use expected from a complete palletizing platform.
With quick recipe setup, built-in conveyors, and an intuitive HMI, TOMA™ Palletizer is designed for manufacturers who want to automate without complexity or custom engineering.
Learn more about TOMA™ palletizer with cobot technology and how it can speed up your palletizing process.
Hybrid Palletizers
Hybrid palletizers combine elements of both robotic and conventional systems to meet specific production needs. They are typically used when a standard solution can’t deliver the required speed, flexibility, or product handling.
Good for: Custom scenarios where neither robotic nor conventional alone is enough.
Pros:
- High flexibility with faster throughput
- Can handle complex pallet patterns or varied product sizes
- Useful for unique layouts or high-speed needs
Cons:
- Higher complexity in design and integration
- Often requires custom engineering and support
How to choose a palletizer that actually fits your plant
Now that you’ve explored the different types of palletizers, it’s time to focus on what actually fits your operation.
Choosing the right system starts with understanding how your line runs today and what challenges you need automation to solve.
Use these questions to guide your decision:
1. What type of products are you palletizing?
Heavy bags, lightweight boxes, irregular containers? The shape, size, and rigidity of your products will determine the kind of gripper you will need and how stable your pallets will be. Start here, it’s the foundation for everything else.
2. How many SKUs do you run, and how often do they change?
If you are switching products or pallet patterns multiple times a shift, you’ll want a system that can adapt quickly without calling in a programmer. Flexibility and ease of changeover matter more than raw speed in these cases.
3. What kind of throughput are you trying to hit?
Your target cases per hour will narrow the field quickly. High-speed lines may justify more specialized systems. Lower volumes or seasonal shifts might benefit more from a modular or redeployable setup.
4. Do you have internal resources to maintain the system?
Highly customized systems often require specialized knowledge, external service contracts, or longer response times when issues arise. If your team doesn’t have in-house automation expertise, or if you can’t afford extended downtime, consider how much day-to-day maintenance and support the system will demand. Standardized platforms are typically easier to maintain internally and faster to recover if something goes wrong.
5. How tight is your floor space?
If your end-of-line is already crowded, look for compact systems with built-in safety or vertical integration. Large conventional systems may not be a fit without major layout changes.
6.Are you looking for a custom system or a ready-to-deploy solution?
Custom solutions can handle just about anything, but they take longer and cost more. Standardized systems are faster to install and easier to train on, especially for teams without automation experience.
7. What’s driving this investment: cost, labor, quality, or all of the above?
Clarifying your core driver helps narrow your options. If labor is your pain point, ease of use and fast deployment might matter more than cycle time. If you’re chasing throughput, speed and uptime should lead.
Take our Configurator Assessment to learn if a standard palletizer like TOMA™ can match your product mix, floor space, and production goals without the complexity of a custom system.
A better fit for modern production
Not every plant needs a fully customized system. And not every standard palletizer is built to adapt. That’s where TOMA™ comes in.
TOMA™ is a standardized robotic palletizer designed to simplify end-of-line automation. It’s built around real production needs: fast setup, intuitive operation, and the flexibility to scale as things change.
- MOVN™ HMI offers one of the most user-friendly interfaces in the industry, no programming required to build or switch pallet recipes.
- The FANUC CRX-30iA cobot handles payloads up to 55 lb (25 kg) and delivers strong collaborative performance with up to eight picks per minute.
- Dual infeed conveyors come pre-integrated, allowing simultaneous palletizing from two separate 4-foot lines.
- Necton™ system monitoring provides live insights to help your team avoid downtime and improve efficiency.
TOMA™ is designed for intuitive robotic palletizing solutions. It is built to help manufacturers reduce complexity, improve consistency, and adapt to change without custom engineering.
Learn more about the TOMA™ palletizer with cobot technology and how it can speed up your palletizing process.
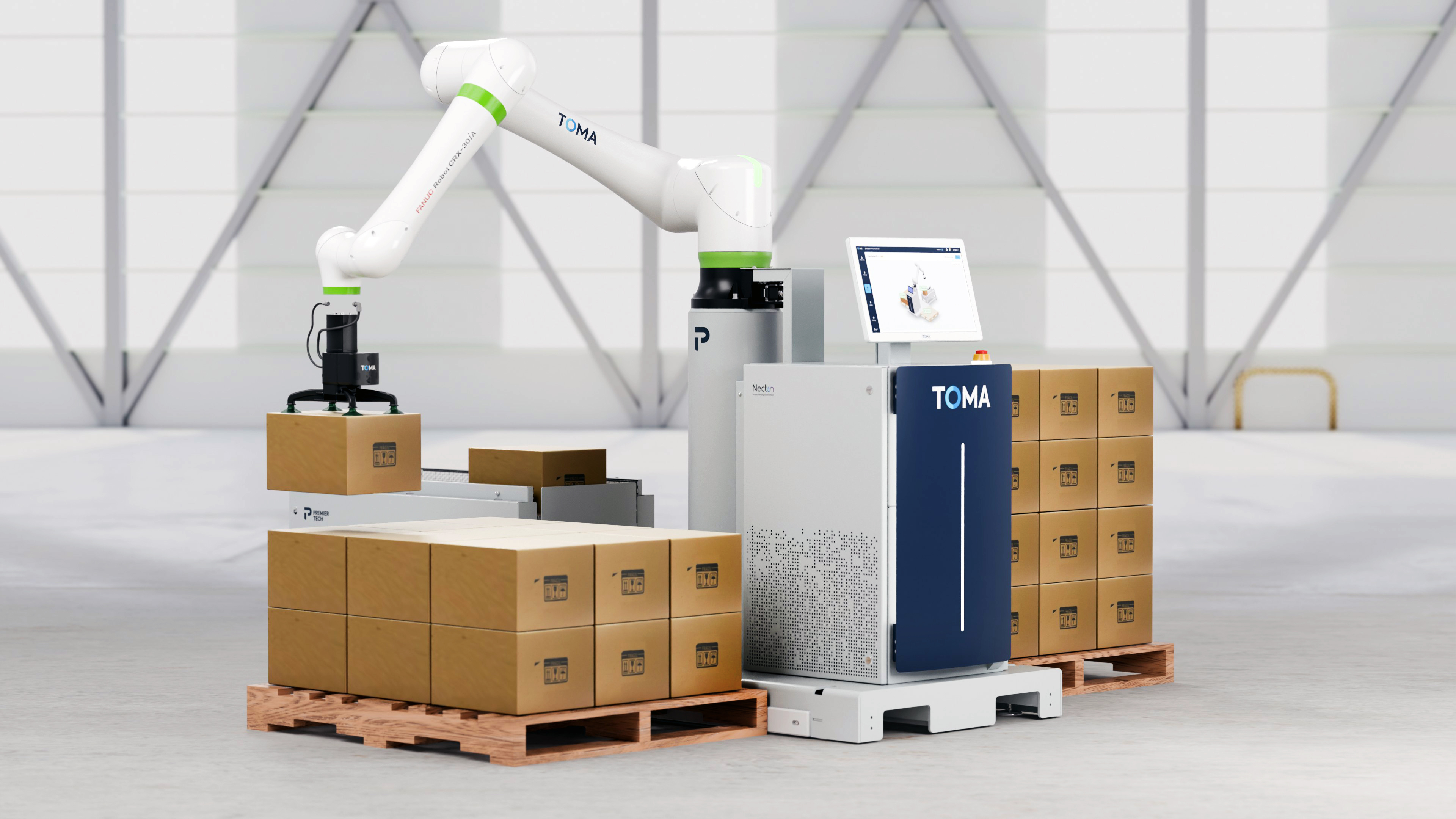
Find The right automated palletizer solution for your operations
The right palletizing system should align with the way your operation runs day to day. It needs to handle your specific product types, fit within your available floor space, and support your short- and long-term production goals.
Whether you are trying to reduce manual labor, increase throughput, or simplify repetitive tasks, the solution you choose should work with your existing layout and scale as your needs evolve.
At Premier Tech, we focus on delivering palletizing solutions that match the way your operation actually runs. Whether you are scaling up, adapting to new product lines, or improving workplace ergonomics, we provide solutions that support your goals and fit your process.
FAQ
The main types are: manual and semi-automatic, conventional, robotic palletizers (including traditional robots, collaborative robots, custom or standard), and hybrid systems. Each type serves different needs depending on volume, product variety, and layout.
Robotic palletizers offer greater flexibility and are ideal for handling multiple SKUs or varied product types. Conventional palletizers are faster for high-volume, single-SKU operations and are mechanically simpler but less adaptable.
Start by evaluating your throughput, product types, SKU variability, available space, and maintenance capacity. The best palletizer is the one that aligns with your current needs and long-term goals. Take our Configurator Assessment
Maintenance varies by type. Conventional systems require routine mechanical upkeep. Robotic systems tend to need less frequent maintenance but may require specialized knowledge or training for certain tasks.
Palletizers are typically installed at the end of a packaging line and can be integrated with conveyors, wrapping stations, and warehouse systems. Modular systems or standard robotic solutions like TOMA™ make integration faster and easier.
Safety should be evaluated across the entire palletizing cell, not just the equipment itself. This includes the end-of-arm tooling, payload size, operating speed, layout of the work area, and how the system is used in practice. Current standards emphasize the need for a full risk assessment and the implementation of appropriate safeguards to ensure safe operation in any environment. Read more in our Palletizing guide article here.
Yes, but not all types can. Robotic systems are best suited for mixed-SKU palletizing due to their flexibility and programmable tooling. Conventional systems are typically designed for consistent, single-product loads.
Ready to find a palletizer that fits your line?
Talk to an automation expert at Premier Tech to explore your options.